
La industria aditiva en Atlas: más ‘smart’ y en busca de materiales más complejos
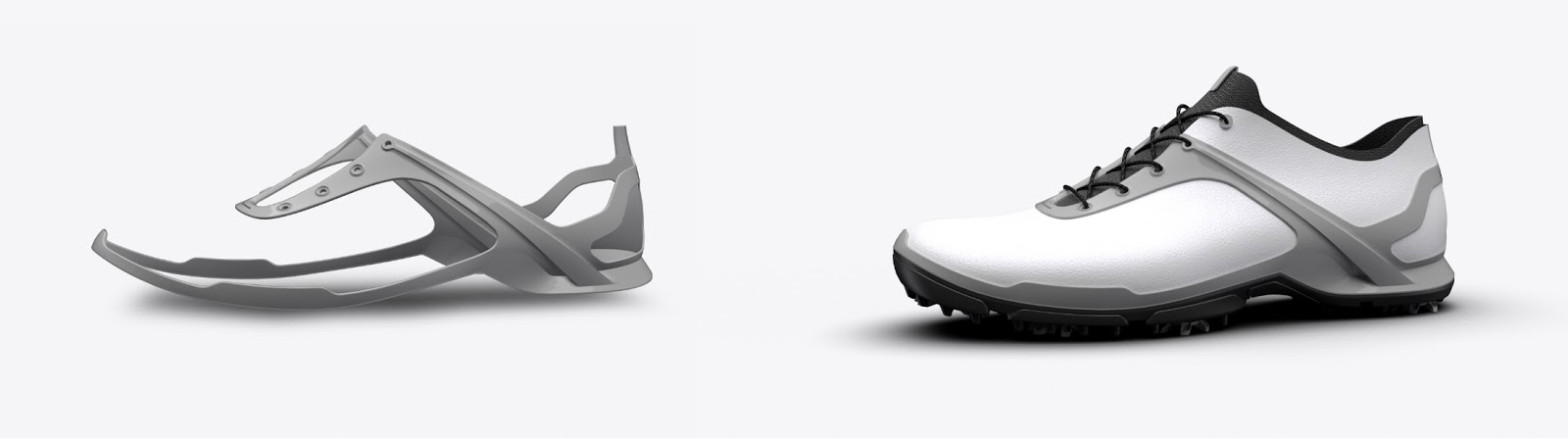
Industrias Alegre, empresa dedicada al suministro de piezas inyectadas para los sectores de electrónica, informática y automóvil, es una de las referencias de Atlas Tecnológico en el ámbito industrial en impresión 3D . Se trata de la primera empresa española y una de las primeras en el mundo en sumarse al reto de la fabricación aditiva en polipropileno de alta reutilización.
El polipropileno es resistente a los químicos, soldable, con baja absorción de humedad y capaz de ofrecer piezas funcionales. Se utiliza poco en impresión 3D por las dificultades que entraña su tratamiento térmico. Industrias Alegre ha unido su conocimiento del sector a la tecnología Multi Jet Fusion de HP y al material proporcionado por BASF para una producción que puede ir desde una única pieza a la fabricación en serie.
Por otra parte, Simplicity Works es una compañía de deep tech que desarrolla una tecnología patentada 3D Bonding, un método que consiste en colocar los materiales en un molde tridimensional terminado y luego, con una inyección de polímero, unir las piezas creando un producto terminado.
3D Bonding elimina la mayor parte del trabajo manual requerido para la fabricación del calzado porque todas las piezas se unen simultáneamente, y no uno por uno como requiere el proceso de costura tradicional (secuencial). Esta tecnología reduce los requisitos de mano de obra hasta en un 70%, logra un 50% de ahorro en el consumo de cuero y tela y disminuye en un 30% el uso de energía de la producción de proximidad. Además, produce un zapato de mayor calidad con mejores prestaciones de comodidad y salud y puede acercar la producción al lugar de consumo.
MADIT está especializada en impresión 3D en metal mediante la tecnología SLM. A partir de polvo metálico, obtiene piezas con geometrías complejas de forma rápida y flexible. La empresa ha colaborado en el montaje de una moto eléctrica de competición universitaria con diseño funcional en coste y tiempo mediante impresión metálica 3D. Se centró en el diseño y la fabricación de componentes de acero inoxidable con el objetivo de optimizar las piezas, aligerar el material de la moto y reducir los tiempos y costes de suministro.
Maflow 3D es la división de fabricación aditiva de la multinacional Maflow, y ofrece un servicio de impresión para prototipos, piezas de uso final y series cortas. Su tecnología de fabricación aditiva Multi Jet Fusion consiste en una plataforma modular compuesta por una impresora capaz de fabricar piezas en ciclos muy cortos junto con una estación de procesado de enfriamiento rápido que mezcla y carga los materiales a utilizar. De esta manera se crea un proceso de producción continuo y se reduce el tiempo de enfriamiento. Entre muchos casos de éxito, ha colaborado con RPA LABS para llevar a cabo un proyecto de personalización de drones comerciales.
Sakata 3D es una marca comercial perteneciente a Polimersia Global, empresa especializada en la fabricación de filamentos para impresoras 3D. Cuenta con un centro productivo en Granada desde donde distribuye su gama de filamentos a nivel mundial.
Altair, por su parte, proporciona software que va más allá de la creación de prototipos únicos con una sólida cadena de herramientas de simulación para mejorar los diseños de productos creados para fabricación aditiva. Su solución Altair Inspire Print3D permite reducir los costes de la fabricación aditiva y el desarrollo del producto al minimizar el uso de materiales, los tiempos de impresión y el posprocesamiento.
Integra múltiples herramientas para diseñar y simular el proceso de fabricación de piezas creadas mediante fusión selectiva por láser (SLM). De esta manera, los ingenieros pueden comprender rápidamente cuáles son los cambios en el diseño o en el proceso que afectan a la eficiencia de fabricación y posteriormente exportar la geometría estructural de piezas y soportes al software de preparación. Además, permite fácilmente detectar y corregir problemas de deformación, delaminación y calentamiento excesivo antes de construir la pieza.
ADDVANCE es una consultora que proporciona asesoramiento sobre la adopción con éxito de la tecnología de fabricación aditiva y su integración con otros sistemas de producción. La empresa ha formado parte de Trenlab, el programa de aceleración impulsado por Renfe, que la ha elegido junto con un grupo de compañías para llevar a cabo su transformación digital y reforzar su posición ante la liberalización del mercado de viajeros en el sector ferroviario.
Por último, Aenium se ha especializado en proyectos en los que la ingeniería de materiales es clave, y utiliza las tecnologías aditivas como tecnologías de conformado láser, aprovechando todas las ventajas de fusión láser para trabajar materiales complejos o conseguir propiedades metalúrgicas más complejos. No se trata de producir series más baratas, sino de trabajar materiales más complejos o hacerlo de una forma diferente.
Fuera del ámbito industrial, el Centro Tecnológico del Mueble y la Madera de la Región de Murcia (CETEM) participa el proyecto ECOADDITIVE que pretende desarrollar y validar un material reciclado a partir de los desechos generados durante el proceso de impresión 3D. Trabaja en la configuración e integración de las tecnologías de reciclado de materiales de impresión 3D, como son el FDM y el PLA, que se encuentran en pleno auge mundial.
El estudio internacional de arquitectura e ingeniería Atanga está centrado en la aplicación de nuevas tecnologías y es experto en fabricación aditiva con desarrollo de materiales (hormigón, yeso, mezclas mixtas y arcillas) así como maquinaría de gran tamaño. En el proyecto 3DCONS se ha involucrado en la innovación en nuevos procesos de rehabilitación de fachadas, paramentos verticales y restauración de elementos arquitectónicos mediante impresión directa, así como sistemas de impresión de elementos prefabricados “a la carta”.
En ambos casos, cada pieza o elemento se crea con total libertad de diseño y optimizando sus prestaciones a las exigencias específicas que tendrá en la fase de uso (formas, espesores, propiedades térmicas y acústicas etc).
Con Hindcon, ha desarrollado una iniciativa de innovación que vincula la metodología BIM de edificios existentes y de nueva creación con su entorno urbanístico desde el punto de vista de las necesidades del individuo. Una de las implementaciones consiste en una impresora 3D de hormigón para piezas prefabricadas a gran escala con sistema de posicionamiento robótico.
Y Cella Medical Solutions desarrolla soluciones médicas utilizando tecnologías de procesamiento de imagen, impresión 3D, realidad aumentada y computación en la nube. Sus soluciones reproducen con precisión los órganos y estructuras anatómicas del paciente, ofreciendo a los cirujanos una ventaja diferencial. Los modelos físicos pueden ser opacos, transparentes o de textura emulada. Entre sus herramientas, navegación intraluminal, resecciones regladas y no regladas, variantes vasculares o volumetrías.
Proyectos destacados

DRUKATT está especializada en la ingeniería y fabricación de piezas funcionales y recambios, principalmente para plantas de proceso o manufactura. Dispone de un servicio de digitalización de recambios, llamado “Recambio virtual”, en el que brinda al cliente la posibilidad de disponer de toda la información necesaria para la fabricación de un recambio, y de esa manera pasar a tener el control del mismo. Uno de sus proyectos destacados consiste en la creación de un protector central de un pulper (hélice) para pasta mecánica, una pieza de 160 kg, la más pesada que ha elaborado la empresa hasta el momento. Se trata del protector central de un pulper de una planta papelera, en la que se ha optimizado su diseño mecánico en la zona de montaje sobre el plato, puesto que los técnicos de mantenimiento se quejaban de que les era complicado realizar el apriete, ya que las llaves no entraban con facilidad.

La multinacional Voestalpine dispone de una red internacional propia de centros de fabricación aditiva avanzada con servicio integral de simulación, optimización, rediseño y fabricación. Sus centros de Canadá y EEUU han sido los primeros de Norteamérica en obtener la certificación de DNV para la industria del petróleo y el gas con el estándar industrial DNV-ST-B203. La certificación cumple con estándares de calidad e integridad de equipos para la fabricación de piezas metálicas impresas. Tuvieron que demostrar con éxito su calificación de proceso de construcción, la tecnología de fusión de metales en lecho de polvo basada en láser (PBF-LB/M) y el tipo de materiales (aleación de níquel de fabricación aditiva).