
De la gota de aceite al baño lubricante
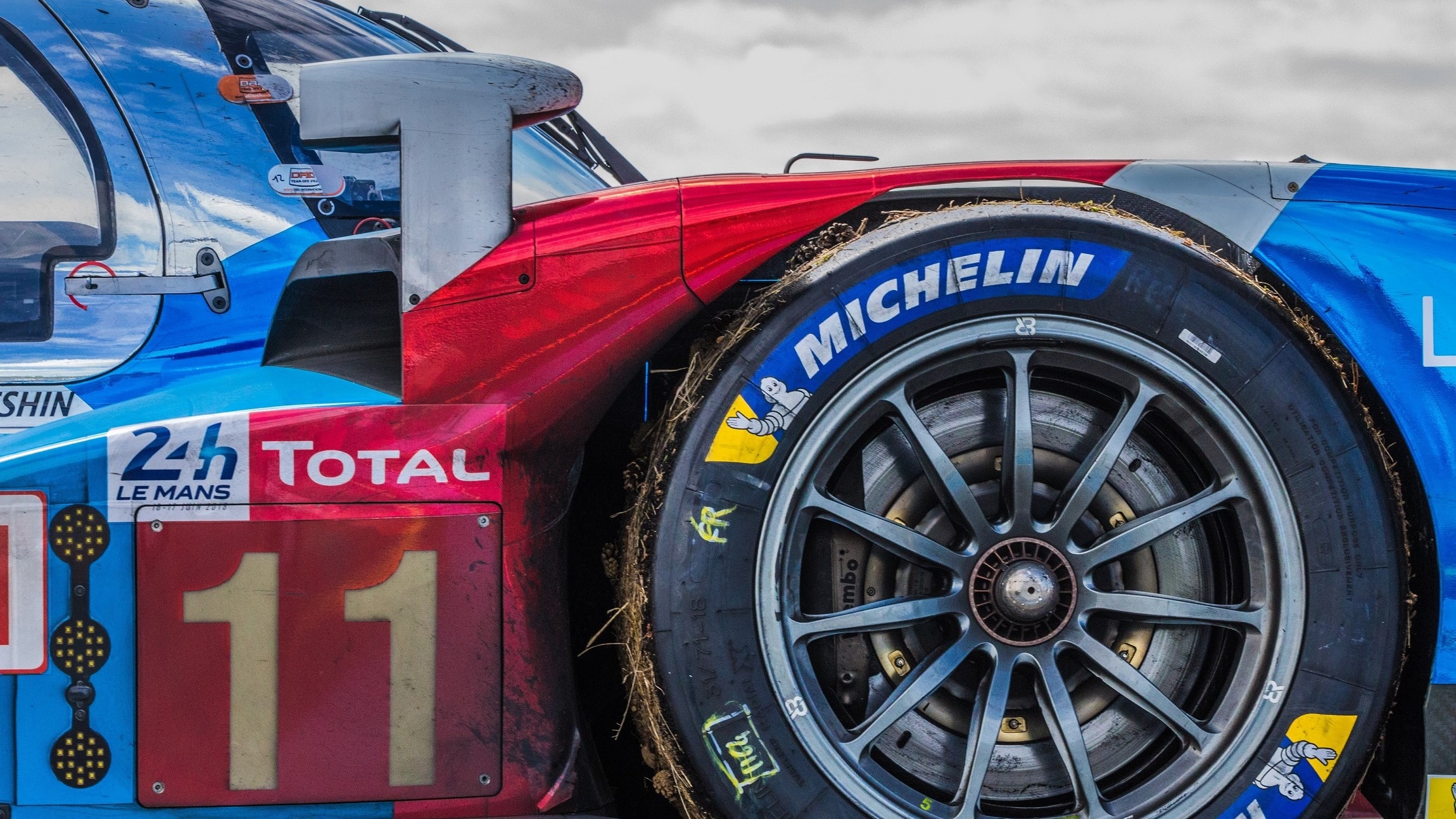
Think big, start small, scale fast (Jim Carroll)
La verdad es que cuando decidimos afrontar un proyecto en el mundo de la industria 4.0 surgen más incertidumbres que en uno tradicional, normalmente más determinista.
El asunto va de datos, sí, de tecnología, también, y sobre todo de personas.
Personas a las que convencer de las bondades del proyecto, no siempre evidentes, para obtener la financiación necesaria.
Personas en las que confiar para crear y desarrollar los útiles tecnológicos que necesitaremos, capaces de comprender con buen sentido, lo que se espera de ellos y, sobre todo, de hacerlos accesibles, realmente accesibles, a los usuarios finales.
Y, por fin, personas que utilicen las nuevas herramientas con convencimiento y les saquen el verdadero partido para que aporten el valor esperado. Este último punto es crucial, porque dará sentido a todo el proceso y lo realimentará para seguir avanzando en nuevas iniciativas.
Para cumplir las expectativas, el lema de Jim Carroll es un buen punto de partida, porque es razonable tener una visión amplia y, sin perderla, empezar poco a poco para tranquilizar conciencias y asumir controladamente los riesgos, esperando, cuando el resultado acompañe, lanzarse a por todo finalmente. Además, suena bien en inglés y eso viste bastante.
Otra forma más prosaica de verlo es la realización de algo que por sí mismo dé un buen resultado y que por su propia naturaleza permita su extensión como un mecanismo en el que la aportación de una gota de aceite haga que, sin darte cuenta, vaya impregnando todo a su alrededor consiguiendo un funcionamiento uniforme.
Esta larga introducción es para poner en contexto una experiencia reciente realizada en nuestra fábrica de referencia, donde hemos implementado un sistema digitalizado de control y eliminación de fugas de aire comprimido que se ha demostrado muy eficaz en procesos de producción clásicos, que utilizan esta fuente de energía.
Lo primero que hay que decir es que el proceso de fabricación de neumáticos está basado en maquinaria compleja y precisa que se basa en muchas de sus partes en elementos accionados por aire comprimido, hablamos de decenas de miles de ellos. El consumo de energía para producir aire es muy significativo, sobre todo, considerando las inevitables fugas, que son por propia definición un despilfarro continuo.
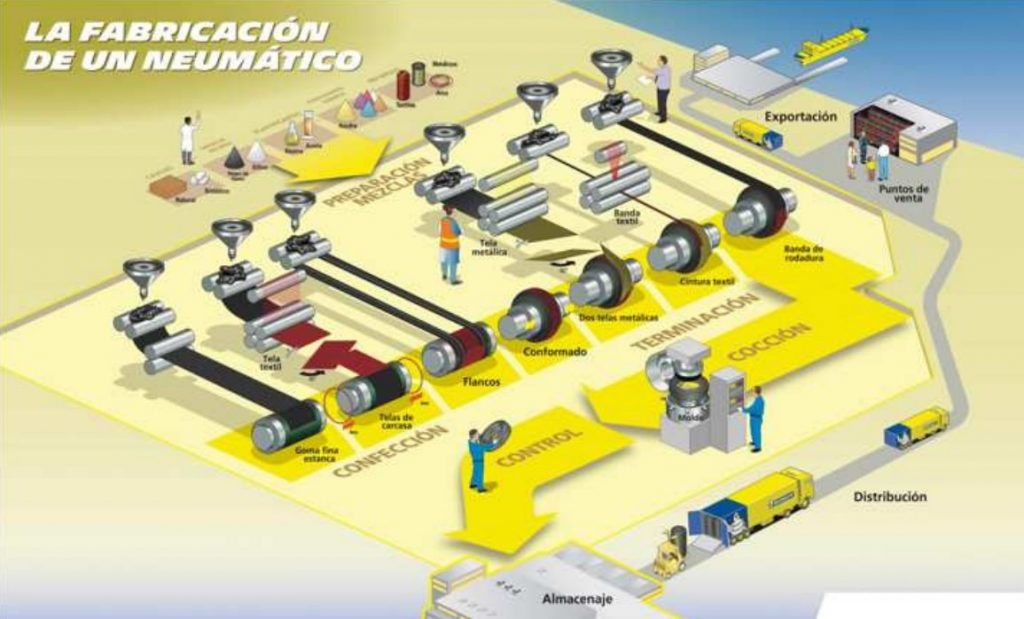
Viendo el proceso completo, la tarea se presenta enorme, pero atacándolo con un principio conceptual válido para todos los casos y aplicable de manera modular y sucesivamente, la solución nos pareció y se demostró, muy interesante. Todo largo camino empieza por un simple paso.
Este era el elemento base. Por otro lado, habíamos definido, con carácter general, en nuestro proyecto de digitalización, una arquitectura para la captación y análisis de datos de proceso: el Datalake. Esto permite, que, con un software, PI Osisoft, podamos controlar las señales provenientes de parámetros de funcionamiento de nuestras máquinas, prácticamente en tiempo real, y con la estructuración de análisis adecuados, podamos extraer conclusiones y realizar las acciones que se necesiten. Esto sería el segundo elemento o condición favorecedora y necesaria.
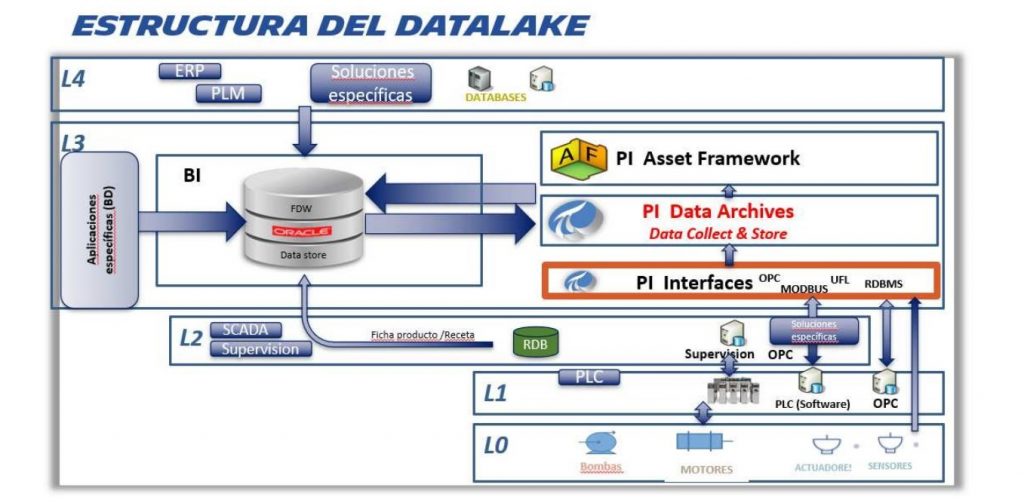
Elegimos empezar nuestro proyecto por una fase del proceso, la vulcanización en prensas autoclave. Siendo satisfactorio el resultado, podríamos justificar su extensión, fase a fase, al resto del proceso.
Esta fase de vulcanización o cocción es especialmente consumidora de aire comprimido. Tiene asignado personal que periódicamente realiza campañas para reducir el volumen de fugas, que en el mejor de los casos mejora un 10% y, en cuanto cesa la campaña, vuelve progresivamente a recuperar el nivel de origen.
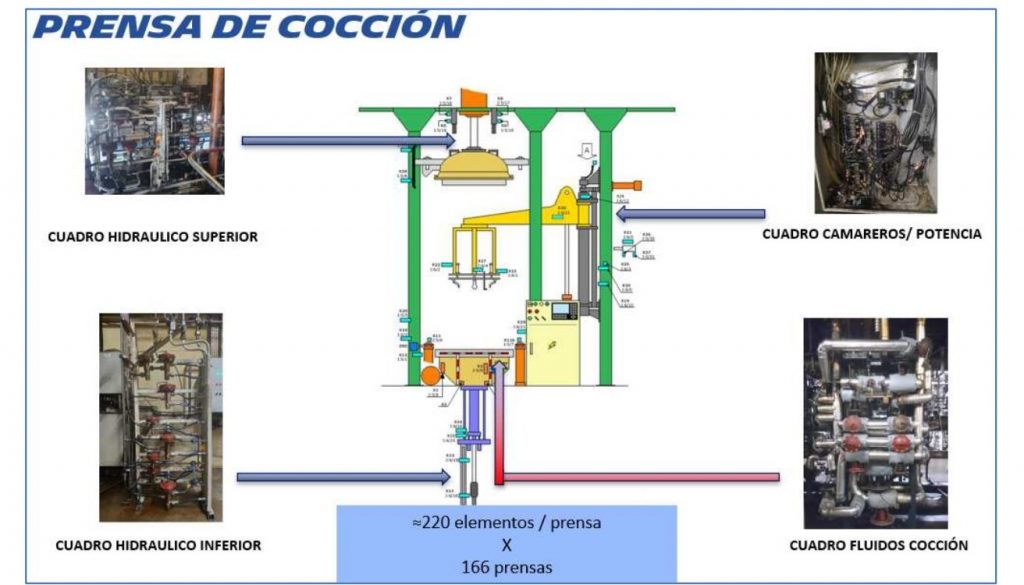
Cada prensa tiene cuatro subconjuntos principales, compuestos por unos 50-60 elementos neumáticos cada uno. Controlar el consumo individualmente hacía prácticamente inviable el proyecto. Se nos ocurrió una idea:
1.- Instalar un caudalímetro conectado al Datalake, que midiera el consumo de aire para cada subconjunto.
2.- Monitorizar el ciclo de máquina, dividiéndolo en secciones y controlando qué elementos entraban en funcionamiento en cada sección, midiendo el consumo de aire de referencia en cada una de ellas y comparándolo con el teórico.
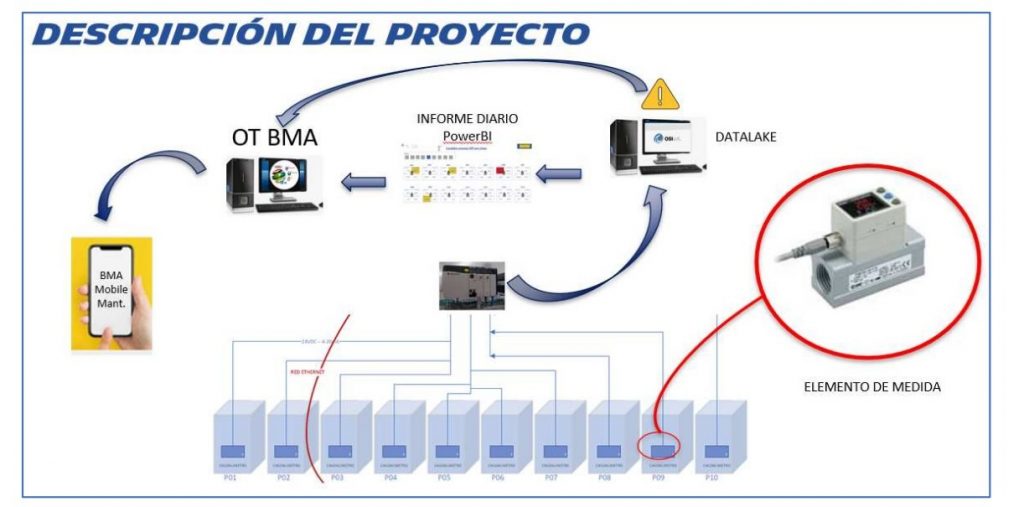
Con esta aproximación, podemos identificar un disfuncionamiento de consumo y asociarlo a un grupo muy reducido de elementos afectados y así dirigir de manera eficaz la acción correctora. Todo esto se implementó con una aplicación gráfica montada sobre PowerBI y fácil de interpretar por los usuarios finales, el personal de mantenimiento.
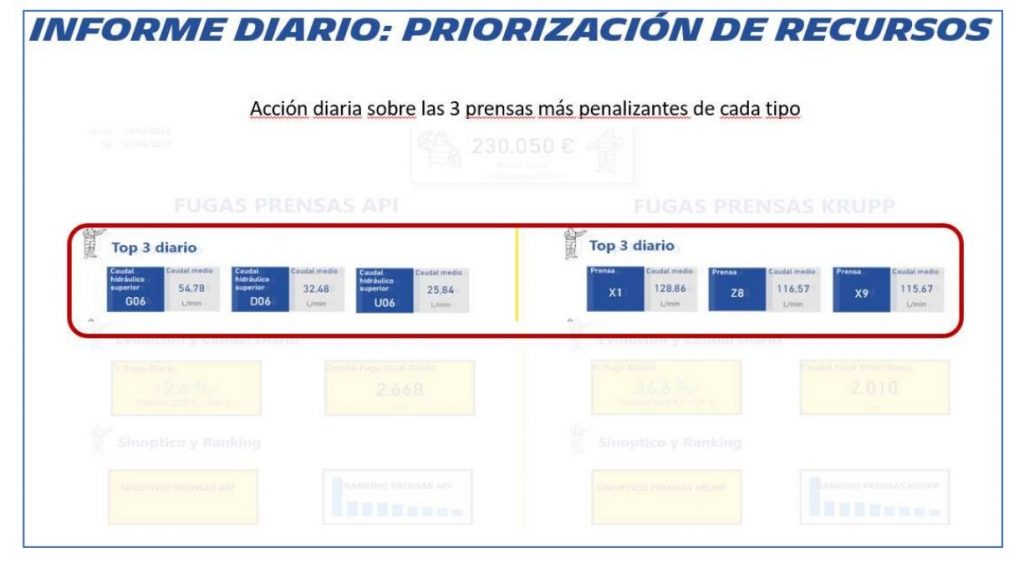
Necesitábamos incluir en su desarrollo el aspecto personal. Para que el sistema funcionara, era necesario integrarlo en los modos de trabajo de los mantenedores de las instalaciones y que estos lo adoptaran como algo útil.
El sistema estaba diseñado para aportar valor en varios ejes, por un lado, la reducción significativa y durable de las fugas de aire, con un interés funcional y de mejora energética. Por otro lado, la comodidad de uso y mejora de las condiciones de trabajo, lo cual está en la base de su éxito de adopción por los operarios. El hecho es que el sistema permite hacer más cómodamente su trabajo y reducir el tiempo dedicado a ello, pudiendo incorporar otras tareas que enriquecen el puesto de trabajo.
Doy, a continuación, algunas claves que justifican el éxito de esta primera aproximación y su aplicación en curso a nuevas fases del proceso:
1.- Reducción efectiva del consumo energético por aire comprimido de más del 40% (antes, solo el 10% sin garantía de continuidad)
2.- Retorno de la inversión de menos de 2 años
3.- Integración en los modos de funcionamiento del personal y mejora de sus condiciones de trabajo
4.- Escalabilidad de la solución, garantizada con una metodología simplificada a todas las fases del proceso y a otras fábricas.
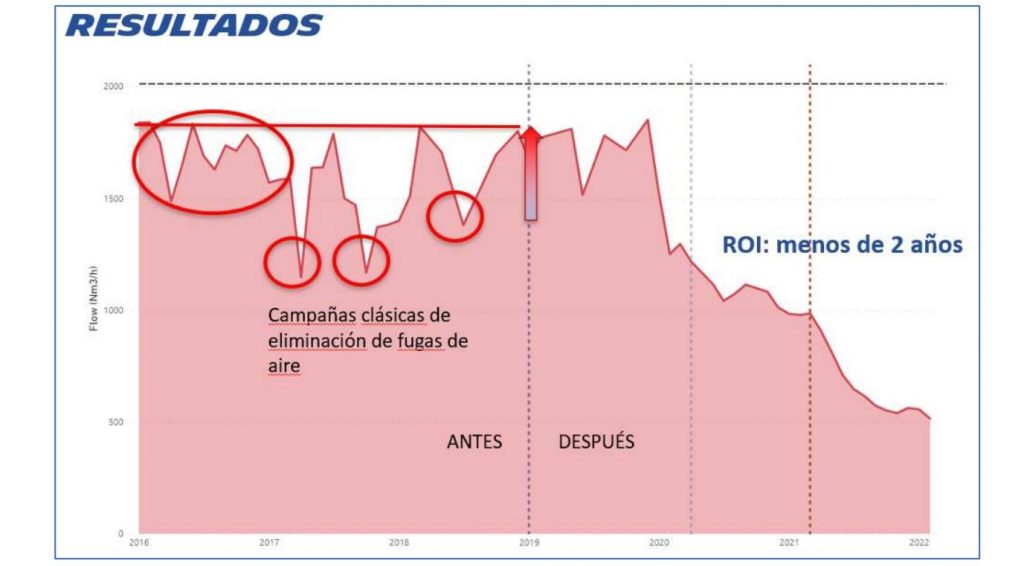
El proyecto está consiguiendo los resultados esperados, ha convencido a no pocas personas con capacidad para decidir, que eran escépticas y, con su primera realización, ha desbloqueado su futuro, dado que, aunque sea claramente rentable, la financiación total para una fábrica, a término, es bastante elevada. Su opción modular, lo hace interesante para su realización por fases.
En definitiva, un ejemplo de pensar en global (THINK BIG), empezar por algo próximo y asequible (START SMALL), y hacerlo generalizable de modo rápido y eficaz (SCALE FAST). O como decía antes, crear lo que sería una gota de aceite y permitir que se pueda extender hasta impregnarlo todo y permitir que el mecanismo funcione perfectamente engrasado.
Germán Arias es director técnico de la planta de Michelin en Valladolid y colaborador de Atlas Tecnológico