
El renacer de la “pesadilla existencial de Henry Ford”
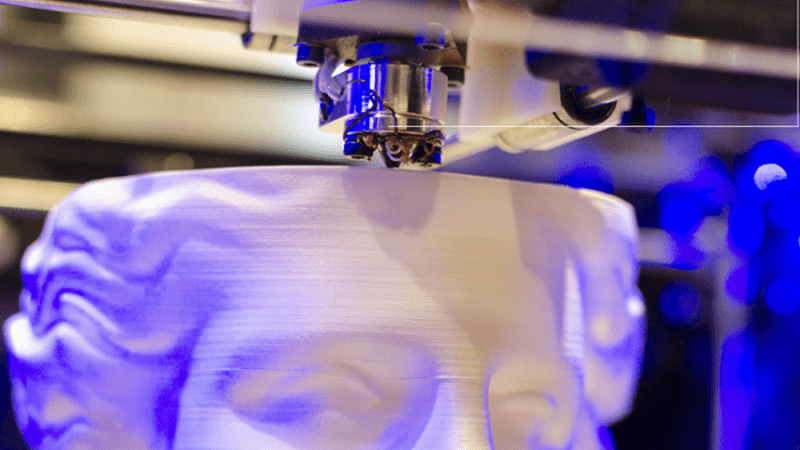
A medida que más empresas adoptan la fabricación aditiva para piezas de uso final y otras aplicaciones, la necesidad de imprimirla correctamente la primera vez y hacerlo a escala, de manera confiable y repetida, está mostrando las brechas que todavía existen en el ciclo de desarrollo del software de diseño, simulación e impresión 3D. En la conferencia Additive Manufacturing Strategies, celebrada en Nueva York, se ha puesto de manifiesto que el futuro de la fabricación aditiva se basará en una mayor simulación de las piezas impresas y del proceso de impresión en sí, así como en incrementar la capacidad de cómputo e inteligencia en planta y durante todo el ciclo de vida del producto.
Un informe de Smartech Analysis asegura que, excluyendo las aplicaciones dentales, se imprimieron aproximadamente 3,5 millones de piezas metálicas en 2020, y casi 1,5 millones de ellas fueron de uso final. Y la demanda seguirá aumentando durante la próxima década, de modo que tanto el software de fabricación aditiva como el de diseño tendrán que evolucionar para satisfacerla.
Si se tiene en cuenta la industria dental, en 2020 se produjeron entre 24 y 25 millones de piezas metálicas impresas en 3D, con el cobalto como tendencia abrumadora. Pero si se excluyen las aplicaciones en odontología, la tecnología de fusión de lecho de polvo es la dominante y el titanio pasa al primer lugar en el uso de materiales. Sus previsiones indican que en 2030 la inyección de aglomerantes metálicos se acabará imponiendo en el mercado de las piezas metálicas.
Igal Kaptsan, gerente general de software de GE Additive, ha incidido en la importancia crítica que tienen para ello los datos y su gestión, dado que la mayoría de los que se utilizan en las aplicaciones de fabricación aditiva se siguen encontrando en silos: en estaciones de trabajo, en impresoras 3D, en el departamento de postprocesamiento… ya no basta con centralizar los datos, sino hacerlo con un modelo común para no generar nuevos problemas. Frente al “desorden distribuido” actual, afirma, la alternativa no debe ser un “desorden centralizado”. Es necesario “definir una capa que sepa qué datos deben venir en qué formato”.
En el caso de la fabricación aditiva crea nuevos tipos de datos que no se pueden gestionar con las herramientas tradicionales de PLM, MES y ERP, y eso puede ser un obstáculo grave en compañías como GE donde una sola impresión puede generar más de 1 TB de datos, explica Kaptsan. Debe producirse en su opinión un cambio de mentalidad, tanto por parte de los OEM de impresoras y como de la industria que las incorpora, para garantizar la visibilidad de los datos asociados a todo el ciclo de diseño y producción.
Siemens Digital Industries está vinculando sus actividades de fabricación aditiva directamente con el concepto de gemelo digital: un modelo virtual de una máquina construida sobre datos de simulación y alimentada con datos que provienen directamente del área de producción a medida que se construye el artículo. De esa manera, “puede asegurarse de que la primera impresión sea la correcta”, según Tim Bell, jefe de CoC. Siemens aprovecha la simulación para ayudar a los clientes a modelar fábricas completas y determinar qué equipo adicional necesitarán y si su enfoque de producción será rentable.
Bradley Rothenberg, CEO y fundador de nTopology, sostiene que “el software en este momento es el cuello de botella. Necesitamos repensar cómo se construye el software de diseño para aprovechar la nueva tecnología y obtener los beneficios en toda la línea de desarrollo del producto”.
Empresas como Autodesk y otras han agregado funcionalidades que facilitan la propagación de cambios de diseño en todos los procesos posteriores, la creación automática de características específicas de aditivos, como estructuras de soporte, y la repetición rápida de simulaciones de procesos.
Jeff Graves, presidente y director ejecutivo de 3D Systems, ha titulado su presentación “El renacimiento de la fabricación aditiva”. La tecnología “ha pasado de ser una curiosidad de laboratorio a fabricar ahora componentes de producción a gran escala en mercados industriales y emergentes”, afirma.
“Después de la pandemia, los CEO de todas las empresas que quieren sobrevivir están reevaluando la cadena de suministro”, asegura. Por eso, la tecnología de fabricación aditiva necesita volverse más robusta, con máquinas inteligentes, autocalibrables, altamente automatizadas y fáciles de usar. Además, las empresas deben poder reunir muchas impresoras 3D y ponerlas en una fábrica trabajando juntas.
La clave para todos estos cambios es la integración flexible, así como un entorno de software que impulse la impresión 3D. Las impresoras 3D también se están volviendo más inteligentes, capaces de configurarse solas, empaquetar densamente piezas para producción y otras tareas. El siguiente paso es, en consecuencia, aprovechar la “inteligencia artificial (IA) en el entorno de software general”. Bart Van der Schueren, CTO de Materialise, coincide en esa apuesta por recopilar datos durante el proceso para ayudar al desarrollo herramientas de inteligencia artificial que ayuden a garantizar una ejecución correcta.
Por cierto que Graves tiene enormes expectativas acerca de lo que está por venir en el ámbito de la impresión de material orgánico real. “Es una tecnología increíble”, dijo. “Creo que este mercado será aún más grande que los mercados actuales. Restaurará la calidad de vida de las personas necesitadas”.
Microfábricas
Tali Rosman es vicepresidenta y directora general de Xerox Elem Additive, y comenzó en Stratasys hace diez años. Hoy en día está entusiasmada con el concepto de microfábrica y su “capacidad para hacer cosas bajo demanda cerca del punto de consumo”. Una idea que aterrizó en el mercado “un poco adelantada a su tiempo”, pero “todo lo que ha estado sucediendo en los últimos dos años”, en referencia a la pandemia, “muestra cuánto se necesita esto ahora”.
La fabricación aditiva puede ser una forma fantástica de agregar agilidad a la cadena de suministro, según Rosman, quien aconseja a los clientes industriales no aferrarse a los materiales exactos que han estado usando, sino preguntar- se por las propiedades de rendimiento de otros alternativos. Optimizar el diseño es fundamental también para reducir la cantidad de piezas y proveedores necesarios y clasificar las piezas de una manera más fácil. Para ello, sostiene, deberíamos hacer que estos sistemas sean más fáciles de usar.
Los problemas vividos en la cadena de suministro pueden convertirse en un dinamizador del sector. Ted Sorom, CEO y cofundador de Mantle, asegura que no ha hablado recientemente con una sola empresa importante de EEUU que no esté lidiando con problemas de la cadena de suministro, “por lo que hay un gran esfuerzo para acercar esta tecnología mucho más a casa”. A juicio de Rosman, cuanto mayor es el punto de dolor, más clientes están listos y dispuestos a “probar la fabricación aditiva”.
Christian Lönne, CEO de Digital Metal, sugiere que, en lugar de centrarse en una sola parte, desde el polvo hasta el postprocesamiento, es necesario observar todo el proceso. “El cambio mental es dar ese salto de fe de la fabricación tradicional a la aditiva”, para lo que “puede ser interesante adoptar algo intermedio, como un sistema híbrido”. Ulric Ljungblad, CEO de Freemelt, cree que los sistemas híbridos son útiles en algunos casos y aplicaciones especiales, pero no en todos. Lo importante es la industria 4.0 y preparar las fábricas para los casos de aplicación de los sistemas de producción en serie.
¿La impresión 3D seguirá siendo un nicho para siempre? El científico jefe de 3D Systems, Brent Stucker, sostiene que la fabricación aditiva ya se usa ampliamente en la producción en masa. Por ejemplo, los alineadores dentales personalizados se producen en volúmenes de decenas de millones al año. La clave es que “las industrias exploren aplicaciones en las que el flujo de trabajo digital y la complejidad de las piezas obtenidas con fabricación aditiva creen ventajas de mercado únicas”.
En cuanto a las posibilidades de integrar la fabricación aditiva en la producción en serie, Chris Schuppe, jefe de ingeniería y tecnología de aditivos de GE, pone como ejemplo que “hemos impreso 100.000 boquillas de combustible en nuestros motores, lo que sin duda supone un buen número para empezar. A medida que observamos el avance de las tecnologías en el espacio del láser y el chorro de aglomerante, vemos que la producción en serie puede pasar de ser de 100.000 unidades en un año a, finalmente, en un mes”.
El vicepresidente sénior de crecimiento estratégico de Stratasys, Pat Carey, piensa de manera similar. “La producción a escala con fabricación aditiva ya está comenzando a suceder. En Stratasys, con una sola impresora podemos producir más de 200.000 piezas en la máquina en un año. Nuestro equipo en Origin, por ejemplo, produjo más de 500.000 hisopos nasales durante el primer pico de la pandemia en 2020. Los analistas predicen que la fabricación aditiva a escala se acelerará en los próximos cinco años y ciertamente contamos con ello”.
Según el directivo, “casi todos los fabricantes la utilizan junto con sus procesos de producción tradicionales. No lo vemos como un ‘o esto o lo otro’ sino como un ‘y’”. Pero ¿se ceñirá a unos pocos verticales, como el cuidado de la salud, o tal vez solo a pequeñas partes de estos verticales? “Existen oportunidades de miles de millones de dólares en aplicaciones como la moda, la odontología, la ortodoncia, los dispositivos médicos, la industria aeroespacial, la automoción, los bienes de consumo o la electrónica. Y debido a nuestra combinación de tecnologías y materiales disponibles, también nos encontramos con la capacidad de ser utilizados en aplicaciones como entretenimiento, artículos deportivos y embalaje”, dice Carey. Estar en todas partes, aunque en forma pequeña, significaría ya “un mercado 50 veces más grande que el actual”.