
La industria 3D deja de lado la comercialización de impresoras para integrar la tecnología en sectores especializados
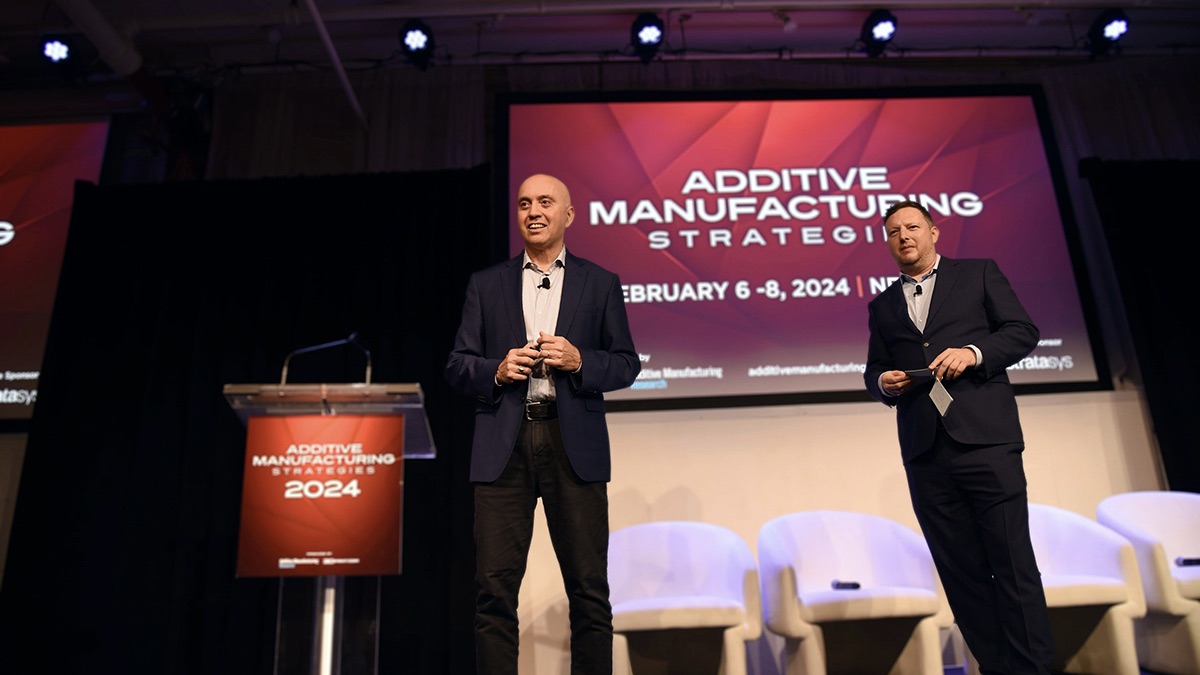
Las innovaciones más disruptivas en impresión 3D han sido reveladas tras la celebración del Additive Manufacturing Strategies 2025 (AMS), un evento de referencia mundial en fabricación aditiva. En los últimos años, la industria se había centrado en el perfeccionamiento técnico de las impresoras 3D para su venta a otras compañías. Sin embargo, esta obsesión por la especificación había dejado en segundo plano un aspecto clave: el desarrollo de soluciones integrales y personalizadas para aplicaciones concretas. Este año, el enfoque ha cambiado radicalmente al redirigir el foco a la reconocida como «integración vertical», que significa la obtención de un control completo del proceso de producción, desde la materia prima hasta el producto terminado. En este marco, la integración del 3D como una tecnología independiente en el resto de industrias vislumbra el futuro de la producción aditiva.
De esta forma, el evento AMS ha dejado en el banquillo al modelo tradicional en el que las empresas ofrecían tecnología sin una aplicación clara en el sector. Empresas como LightForce Orthodontics han sido objeto de este viraje, pues ha dejado de vender impresoras 3D como producto principal y comenzado a utilizarlas internamente para fabricar piezas con aplicaciones de alto valor en su industria. En su caso particular, el sector de la ortodoncia, a través de la impresión 3D de brackets personalizados, lo cual, además, desafía el estándar del modelo por inyección y permite una mayor personalización en el sector médico. En general, esta edición ha estado marcada por un tono más realista y data-based, en lugar de proyecciones especulativas.
Esta transformación también ha cambiado la manera en que las empresas monetizan la impresión 3D. En lugar de vender impresoras y consumibles, ahora muchas han fijado sus precios en función del valor generado para el cliente. Como ha explicado Jeff Herman, CEO de Fabric8Labs, su empresa puede mantener márgenes saludables al ofrecer piezas más eficientes y competitivas frente a la fabricación tradicional, sin necesidad de vender impresoras a terceros. Este modelo de negocio permite a las compañías controlar mejor su tecnología, evolucionarla continuamente y asegurar que responde a necesidades reales del mercado.
Otro ejemplo de este cambio de enfoque es BMW, que está utilizando fabricación aditiva para optimizar la producción de piezas en polímeros y metales. La compañía ha apostado por materiales abiertos de bajo coste comprados directamente a proveedores químicos, lo que le permite fabricar componentes de hasta 8 kg, todos ellos diseñados de manera aditiva para reducir peso y mejorar rendimiento. Además, su estrategia se centra en la automatización y estandarización, por lo que integra la impresión 3D con el mantenimiento industrial convencional, el software de ingeniería y los flujos de producción. Cuanto más alineada esté la impresión 3D con los procesos de fabricación tradicionales y las necesidades específicas de producción, mayor será su impacto real en la industria. De hecho, Scott Dunham, vicepresidente ejecutivo de AMR, destacó, «la industria debe centrarse en desarrollar soluciones con impacto real en el mercado y no solo en promesas futuristas».
Y, a medida que la impresión 3D se integra con la manufactura avanzada, la automatización y la producción en masa también atraviesan una metamorfosis. Empresas como Seurat Technologies han perfeccionado un sistema de impresión de piezas metálicas a gran escala, lo que les permite competir directamente con procesos tradicionales como la fundición (un proceso donde el metal fundido se vierte en moldes) y el mecanizado (que implica cortar o dar forma a los materiales). De esta forma, no solamente producen piezas finales con alta precisión, sino que también lo hacen de manera más eficiente y rentable. Así, empresas como Siemens Energy y Honda pueden utilizar la impresión 3D para producir componentes metálicos de gran volumen con los mismos estándares de calidad que ofrecen los métodos tradicionales, pero con la ventaja de mayor flexibilidad en el diseño y reducción de costes. Este modelo permite que la impresión 3D deje de ser una herramienta exclusiva para prototipos y pase a sostener la producción en serie de piezas finales.
La colaboración también ha emergido como un tema clave en AMS 2025. Empresas como HP, a través de Alex Moñino, han subrayado la importancia de alianzas estratégicas para superar barreras en la industria. Modelos como el Consorcio Leading Minds o MGA Mobility buscan reunir a fabricantes y proveedores en sectores específicos, como el ferroviario, la marina o la defensa, para compartir costes y estandarizar procesos. La Directora General de Mobility/Medical Goes Additive, Stefanie Brickwede, señala, «estas colaboraciones pueden acelerar la adopción de la fabricación aditiva en sectores altamente regulados».
Sin embargo, todavía existen retos para la implementación de estas soluciones. Como sea ha destacado en el Additive Manufacturing Strategies 2025, la clave para el éxito no es pensar en la impresión 3D como una industria independiente, sino como una tecnología dentro de las industrias de los clientes. Es decir, cuanto más enfocadas sean sus aplicaciones, mayor será su adopción y valor. Existe una necesidad urgente de mejorar la eficiencia en todas las industrias, y la impresión 3D, cuando se integra estratégicamente con otras tecnologías de producción avanzada, tiene el potencial de marcar una diferencia disruptiva en la fabricación global.