
Capacitar al trabajador conectado: la próxima evolución de la Industria 4.0
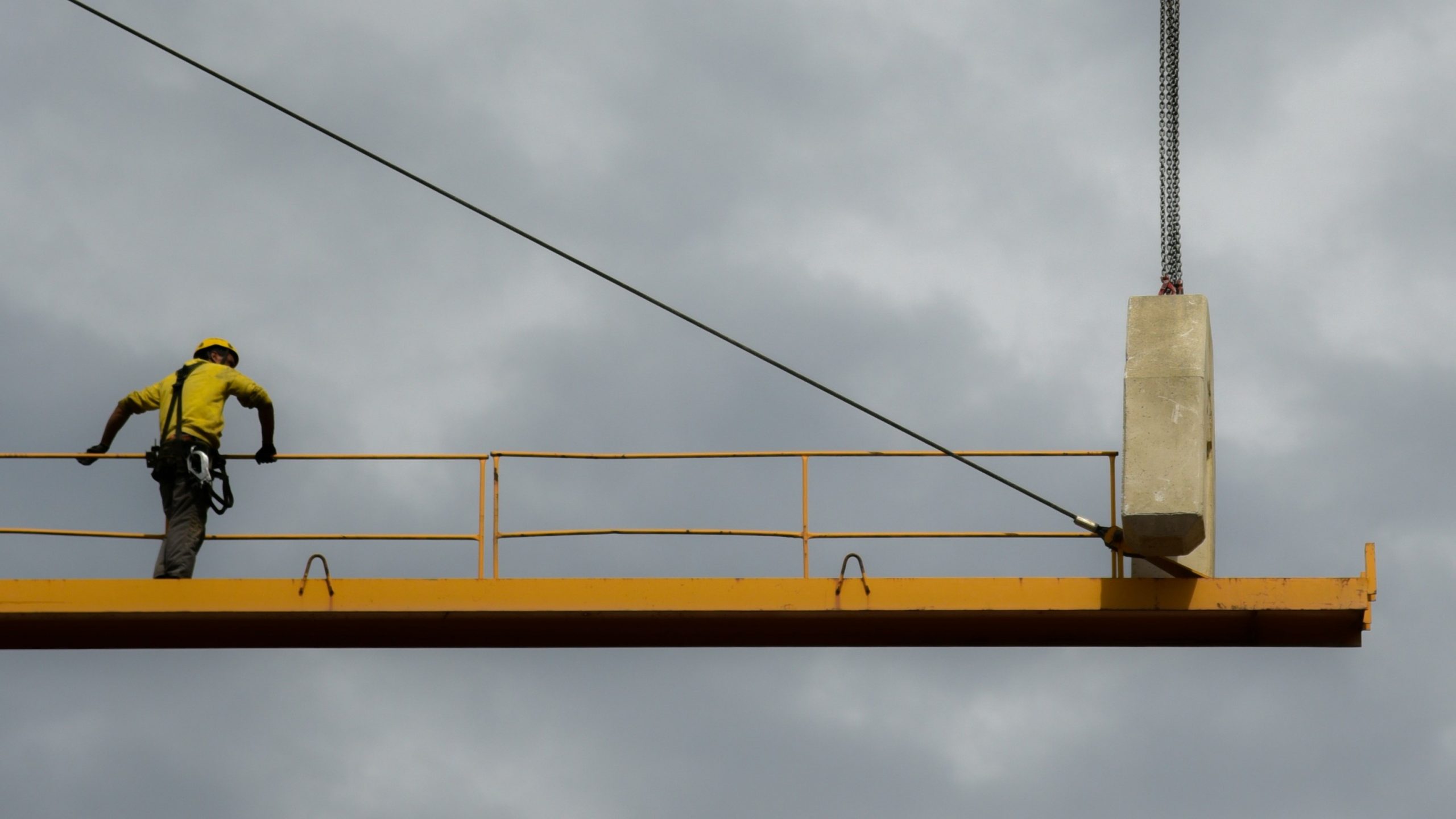
Desde su introducción hace una década, la Industria 4.0 se ha convertido en una realidad. Hoy en día, las tecnologías digitales, la automatización, la robótica, el análisis de datos y el Internet de las cosas (IoT) están creando empresas de fabricación más eficientes, flexibles e inteligentes. La Industria 4.0 también está permitiendo la automatización de tareas repetitivas, la reducción de lesiones en el lugar de trabajo, una mayor productividad y productos de mayor calidad.
Los beneficios de la Industria 4.0 se necesitan con urgencia en un momento en el que las organizaciones se enfrentan a muchos retos de mano de obra a medida que los fabricantes navegan por las iniciativas de transformación digital e industrial: escasez de talento, la creciente brecha de habilidades, el envejecimiento de la fuerza laboral y los continuos desafíos de la cadena de suministro global. Para superar estos retos, el cambio a una fuerza de trabajo digital puede ayudar a empoderar a las nuevas generaciones de la mano de obra de primera línea.
Capacitar con datos a los trabajadores de primera línea
La clave de esta capacitación de los trabajadores de primera línea son los datos. Los datos recogidos de sensores y equipos pueden permitir el mantenimiento predictivo; los datos de formación pueden ayudar a los trabajadores a seguir procedimientos operativos seguros; y los datos impulsan la IA en la cadena de montaje para identificar problemas de calidad del producto antes de que lleguen a los usuarios finales.
Quizás por primera vez, los datos se están convirtiendo en el ámbito del trabajador de primera línea. El papel del trabajador conectado, integrado en su entorno de trabajo a través de la tecnología, se ve potenciado por los datos y acelera el flujo ubicuo de datos en toda la empresa.
Según Deloitte, «las organizaciones pueden lograr beneficios tangibles elevando la experiencia digital del trabajador de primera línea y empoderando a su fuerza de trabajo de primera línea con la tecnología, las herramientas y la información necesarias para el trabajo.» También explican: «Cuando a los trabajadores de primera línea se les proporciona una combinación reflexiva y estratégica de tecnología para realizar su trabajo, la productividad aumenta de media un 22%.»
Armados con herramientas digitales como aplicaciones móviles, dispositivos electrónicos, automatización e IA, los trabajadores conectados no solo están impulsando su productividad, seguridad y eficiencia en la fábrica, sino que también se están empoderando con la información y las herramientas que necesitan para tomar decisiones informadas y mejorar su rendimiento.
Con estas herramientas, pueden comunicarse en tiempo real, acceder a datos y colaborar con otros trabajadores, máquinas y sistemas. Y el futuro del trabajador conectado está empezando a perfilarse.
La próxima evolución de la Industria 4.0
A pesar de todos los grandes avances y adelantos digitales de la Industria 4.0, faltaba una pieza del rompecabezas: cómo integrar los datos, la información y las operaciones de la planta de fabricación en la empresa en general. Todo comienza con el trabajador conectado.
La integración de los datos de los trabajadores conectados con otros flujos de datos de la empresa permite tomar decisiones empresariales más informadas y rápidas a escala gracias a una visión de 360 grados de la empresa. Esta conectividad permite a los trabajadores de la planta de producción colaborar con las operaciones de la línea de negocio para tomar decisiones más rápidas, precisas e impactantes en toda la organización.
Todo empieza en la planta de producción
Consideremos el siguiente escenario. Gracias a un sistema de mantenimiento autónomo, un trabajador de la fábrica descubre que las tapas de los vasos de yogur no cierran correctamente. Crea un informe en una plataforma de software para trabajadores conectados, que automáticamente crea un evento de calidad en el sistema de gestión de la calidad de la empresa, lo que da lugar a una investigación o a la puesta en marcha de procesos de calidad clave, como una acción correctiva y preventiva, una solicitud de acción correctiva del proveedor o una no conformidad. Una vez realizada esta investigación, podrían identificar que el proveedor ha cambiado la composición del adhesivo de las tapas de los yogures. Entonces alertarían automáticamente al resto de centros y enviarían instrucciones a cada planta de la fábrica para calentar las tapas 10 grados más.
A través de un flujo de trabajo automático en todo el ecosistema de la empresa, los seres humanos interactúan con la tecnología para revolucionar los procesos de fabricación, impulsar la toma de decisiones basada en datos y permitir la mejora continua.
Otro ejemplo es lo que conocimos en el Collaborate de Zaragoza. Una solución que nace de la colaboración dentro del ecosistema de Atlas Tecnológico. Tres compañías, MesBook, TST Sistemas y TLSI presentan una solución que es un claro ejemplo de capacitación del trabajador conectado. El concepto engloba la aplicación integrada de tecnologías avanzadas en la gestión interna de almacenes y centros de distribución. Se centra en abordar la integración y sinergia entre el geoposicionamiento (para rastrear la ubicación precisa de productos), la trazabilidad (para seguir el movimiento de los productos a lo largo de la cadena de suministro), la automatización (para realizar tareas de forma autónoma o semiautónoma) y la gestión de stocks (para optimizar el control y la reposición de inventario). El resultado de combinar estas tecnologías, las empresas pueden lograr una mayor visibilidad, precisión y eficiencia en la gestión de sus operaciones logísticas internas, lo que les permite satisfacer mejor las demandas del mercado y mejorar la satisfacción del cliente.
Las herramientas digitales del oficio de trabajador conectado
Del mismo modo que la Industria 4.0 no se hizo realidad de la noche a la mañana, el siguiente nivel de su evolución, el empoderamiento del trabajador conectado, también tardará en materializarse. Considere los siguientes pasos que las empresas pueden dar para lograr una empresa verdaderamente conectada, desde la alta dirección hasta el trabajador de primera línea.
· Empiece por identificar el problema. Toda iniciativa digital comienza con un problema que hay que resolver. Es importante definir primero los verdaderos cuellos de botella y qué se entiende por éxito. Tal vez el problema sea que los ciclos de producción son demasiado largos, los empleados no ven el panorama general o la seguridad se ha quedado atrás en la fábrica. Una vez identificado el problema, realice una evaluación exhaustiva de los procesos actuales, la infraestructura tecnológica y las competencias de los trabajadores para identificar las áreas que pueden beneficiarse de la tecnología.
· Invierta en formación. Es fundamental formar a los trabajadores de primera línea en los conocimientos necesarios para manejar y mantener tecnologías avanzadas. Igual de importante es disipar la preocupación de que la tecnología quite puestos de trabajo, demostrando que la tecnología es un conducto hacia un mayor éxito y capacitación individual.
· Realice una auditoría de datos. Determine dónde residen todos sus datos dentro de diferentes sistemas y silos. A continuación, recopílelos e intégrelos para facilitar el acceso del trabajador conectado. Adoptar soluciones basadas en la nube puede permitir un fácil acceso a ellos desde diferentes ubicaciones y facilitar la colaboración.
· Recopilar experiencias de usuario. La tecnología es crucial para atraer a la próxima generación de talentos de fabricación, pero también tendrá que tomar continuamente el pulso al personal para abordar cualquier frustración o comentario positivo sobre las soluciones para corregir continuamente el rumbo.
· Aprovecha las colaboraciones. Al colaborar con proveedores de tecnología, startups y otros socios del sector, puedes ponerte al día de los últimos avances e innovaciones en Industria 4.0. Las asociaciones también pueden proporcionar acceso a conocimientos y recursos.
· No olvide la seguridad. Centralizar y abrir los datos críticos de toda la empresa puede plantear problemas de ciberseguridad. Es importante implantar medidas de ciberseguridad sólidas para proteger los datos y sistemas sensibles frente a las ciberamenazas.
El objetivo de la era de los trabajadores conectados de la Industria 4.0 es permitir que los seres humanos impulsen una mejor calidad, seguridad y productividad más allá de las paredes de la fábrica, aprovechando la tecnología adecuada en el momento oportuno para construir y cambiar procesos y flujos de trabajo. Con ello y los datos derivados de esos cambios, toda la organización se transforma, se revitaliza y se fortalece.
Pero todo empieza con el ser humano conectado, comprometido y capacitado: el trabajador conectado.