
Rubén Ramírez insta en La Hora Premium a incorporar la «cultura del no fallo» para asegurar el éxito del mantenimiento predictivo
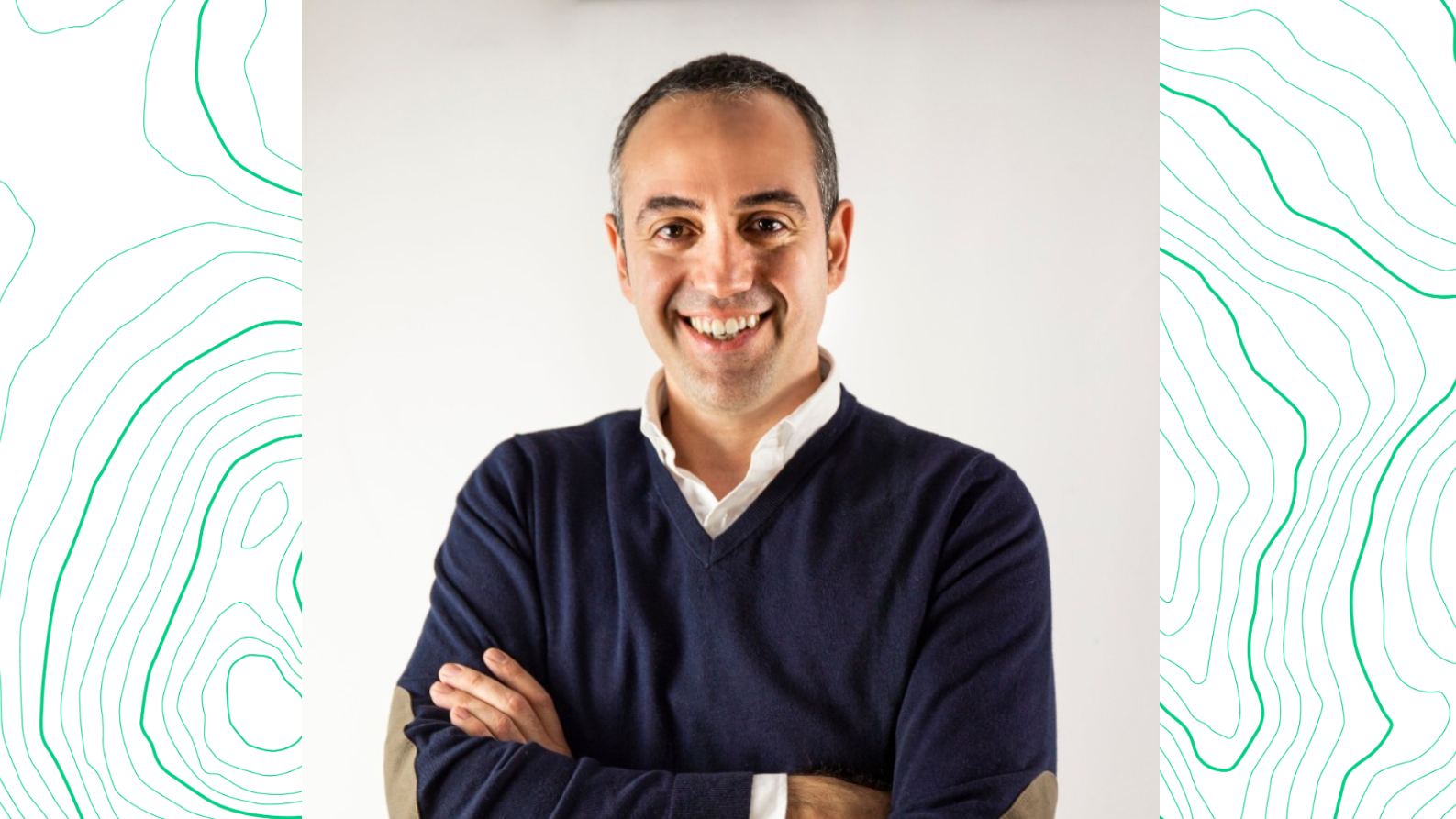
El CEO y cofundador de Dira Reliability, Rubén Ramírez, ha participado en ‘La Hora Premium’ con una ponencia titulada ‘Desde los orígenes a los nuevos paradigmas del mantenimiento predictivo’, con la que ha inaugurado el nuevo ciclo temático. Ha defendido la necesidad de incorporar “la cultura de la fiabilidad en la empresa” para asegurar el éxito de la introducción de herramientas de mantenimiento predictivo. “Es un concepto muy importante que hay que empezar a manejar, es la cultura del no fallo”, ha explicado. El mantenimiento predictivo “no es solo tener una aplicación de monitorización de vibraciones, sino que la clave es coordinar las acciones correctivas de la máquina con la vigilancia del parámetro”.
Ramírez ha iniciado su ponencia definiendo el concepto de mantenimiento predictivo como una “metodología para detectar e identificar fallos en activos industriales en su fase incipiente. Se consigue mediante la aplicación de técnicas no intrusivas que permiten conocer el estado o la condición de la máquina sin necesidad de interrumpir su operación”, ha concretado. El CEO ha mencionado las técnicas más conocidas, como el análisis de vibraciones con sensores, la termografía, los ultrasonidos o los análisis de aceite.
Tras esta introducción, Ramírez ha compartido información sobre los orígenes del mantenimiento predictivo. Ha mencionado las incipientes iniciativas de la industria naval americana, en los años 50 y 60, que fue pionera en investigar técnicas que les permitieran conocer la condición de la máquina para aligerar las enormes partidas presupuestarias en mantenimiento. “Paralelamente, la armada soviética desarrolló en los años 60 y 70 sus programas de mantenimiento predictivo; en esa época ya eran capaces de medir la alta frecuencia de la vibración, que es lo más difícil”, ha explicado. “Ambas potencias se estaban preparando para un eventual conflicto bélico y querían que sus flotas navales tuvieran la máxima preparación, por lo que establecieron políticas para sustituir el mantenimiento basado en horas en el predictivo”, ha asegurado.
Claves del éxito
Tras este repaso histórico, Ramírez ha compartido las claves del éxito para cualquier programa de mantenimiento predictivo. En primer lugar, ha destacado esa incorporación de la cultura de la fiabilidad en la empresa. “En Fórmula 1, por ejemplo, de nada sirve ser en 49 vueltas el más rápido si en la 50 te quedas parado; y en industria es lo mismo”, ha defendido. “Esa cultura del no fallo hay que introducirla desde el principio en la empresa, y está muy relacionada con el mantenimiento predictivo”, ha asegurado.
En este sentido, ha compartido algunos datos de un informe de McKinsey, que defienden que aplicando técnicas de mantenimiento predictivo “puedes lograr entre un 5 y 15% de mejora en la disponibilidad de los activos, y reducir entre un 18 y un 25% los costes de mantenimiento. Estos fueron los KPIs que impulsaron a la industria naval americana a implementar mantenimiento predictivo hace 70 años”, ha dicho.
El experto también ha explicado la curva P-F, que muestra la evolución desde que aparece el fallo potencial hasta el fallo funcional. “Coordinar la acción correctiva con la vigilancia del parámetro es una de las claves de un buen mantenimiento predictivo”, ha asegurado, y ha explicado que esto “permite programar una parada una vez tenido el fallo potencial y antes de que ocurra el funcional, seleccionando cuál es el mejor momento para parar la máquina”.
Evolución y consejos
También basándose en McKinsey e introduciendo más información, Ramírez ha hablado sobre la evolución del mantenimiento predictivo, que ha establecido en cuatro fases. La primera es la de generación de alarmas sobre umbrales predefinidos que informe de eventos de la máquina, a lo que le sigue la detección e identificación de defectos mediante freciencias y bandas de análisis. Un tercer estadio sería la monitorización específica de modos de fallos a través de parámetros predictivos y de proceso, mediante machine learning con modelos entrenados de eventos anteriores. “Tener este histórico es lo difícil, pero el verdadero valor es combinar parámetros predictivos y de proceso”, ha defendido.
La última fase sería cuando el mantenimiento predictivo y los gemelos digitales conviven simultáneamente. “Es cuando tienes datos de mantenimiento predictivo de diferentes máquinas o de plantas completas, datos de proceso, gemelos digitales y haces simulaciones en tiempo real de posibles escenarios”, ha explicado. “En este nivel no están muchas empresas; algunos son los fabricantes de maquinaria”, ha añadido.
El CEO de Dira Reliability ha mencionado aquí un ejemplo de un gran pionero del mantenimiento predictivo en España en el sector ferroviario: el Metro de Madrid. “Tenían que acometer muchas sustituciones de reductores al año, que repercutían en una partida presupuestaria muy alta en partes de repuesto”, ha expuesto. “Tras acudir a diversos congresos internacionales, su dirección fue pionera en España en introducir análisis de vibraciones mediante equipos portátiles que buscaban patrones de defecto en esos reductores”.
Ramírez ha añadido que, con las nuevas tecnologías 4.0, la medición “se ha visto fomentada por dispositivos IoT, y el análisis ponderado por plataformas web y sistemas cloud. Se puede mejorar mucho mediante el uso de técnicas de IA o machine learning, pero hay que empezar a capturar datos y tener eventos y patrones sobre los que la IA pueda aprender”.
El experto ha compartido, también, algunos consejos para empezar a utilizar el mantenimiento predictivo en las industrias. En este sentido, ha hecho hincapié en la necesidad de incorporar la cultura de la fiabilidad y en no “obsesionarse con los resultados a corto plazo y con la tecnología. Es un camino a medio-largo plazo”, ha asegurado. Además, ha destacado la idoneidad de buscar “un buen compañero de viaje, que te asesore en una buena implementación y te integre las tecnologías que necesitas”. También ha mencionado la necesidad de realizar “una matriz de criticidad de los activos, porque el mantenimiento predictivo debe hacerse en función de la probabilidad del fallo y de sus consecuencias. Al final, debe ser rentable donde lo vayas a implementar”.
En el turno de preguntas y respuestas, el experto ha defendido que el mantenimiento predictivo “debe estar alineado con el departamento de mantenimiento”, no ir liderado únicamente por el departamento de IT.
Para finalizar, Ramírez ha explicado que el mantenimiento predictivo “se ha democratizado mucho” gracias al abaratamiento del hardware y de los sensores. “Empresas manufactureras ya se plantean implementar estas técnicas en sus plantas industriales, algo impensable hace 10 años”, ha concluido.
Tras la ponencia de Rubén Ramírez , en el ciclo participará también Antonio José Conesa, responsable del Departamento Técnico de Henkel Ibérica, quien compartirá la ponencia titulada ‘Soluciones de mantenimiento 4.0 que aumentan la fiabilidad en las instalaciones industriales’. Tras él, será Ángel García Bombín, Industrial Digital Transformation Director en Sonae Arauco, quien ofrecerá la ponencia ‘Uso de sistema PdM integrado en la organización’. El ciclo finalizará con una mesa redonda titulada ‘Diferentes perspectivas del mantenimiento predictivo’, en la que participarán Beltrán Blázquez (Cofundador y CEO en Synnect), Borja López (HO Industrial Means Maintenance WLCA350 en Airbus), Román Martín (COO & KAM en LIS Data Solutions) y Xavier Riba (Cofundador y Sales Manager en Innovae y colaborador en Atlas Tecnológico).