
Rubén Ramírez (Dira) rebaja el suflé de la IA: «sin datos y un histórico de eventos no se puede»
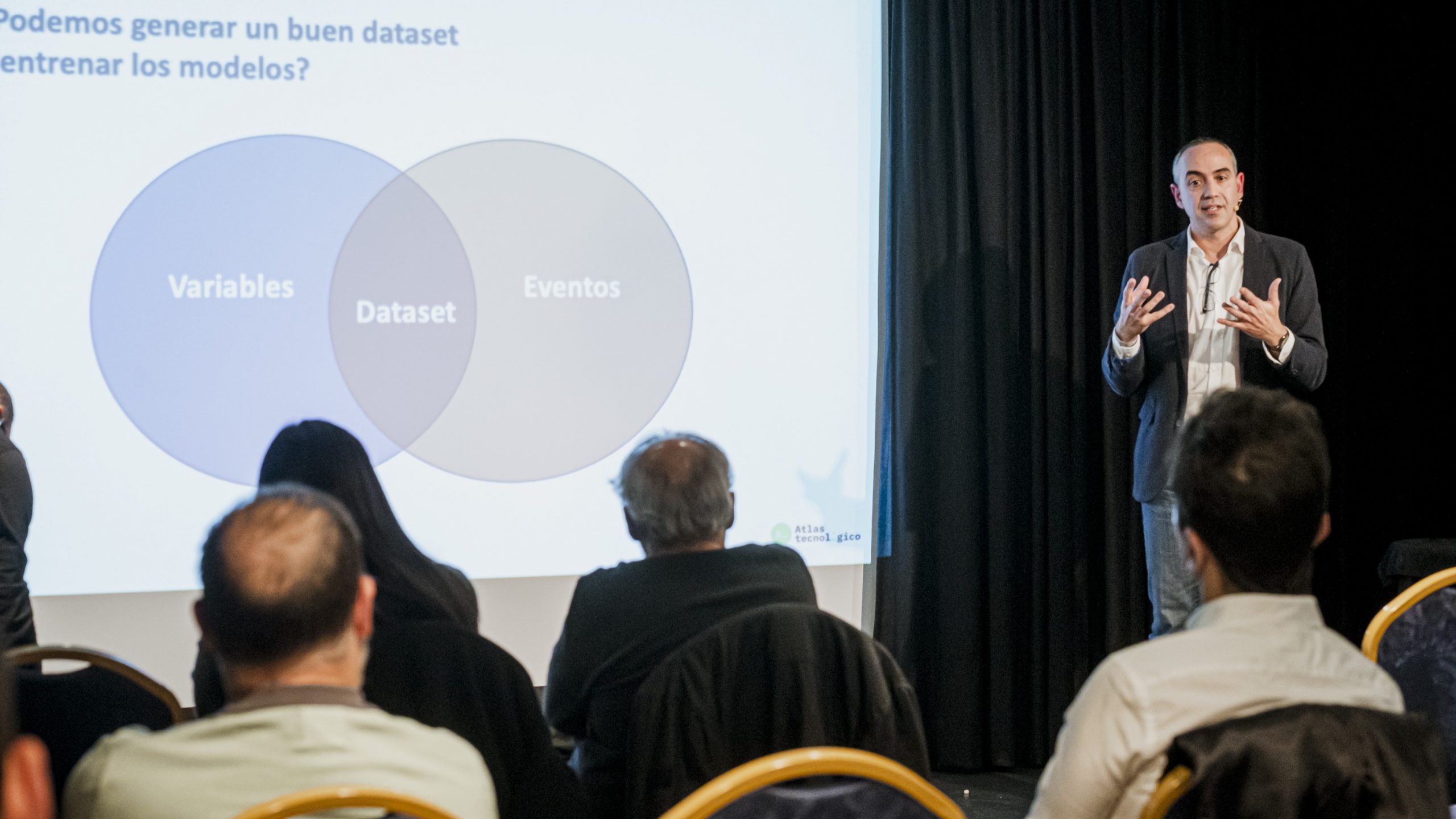
El CEO de Dira Reliability, Rubén Ramírez, explica en la cuarta jornada de New in Valencia una experiencia de éxito de su empresa en mantenimiento predictivo, “lo que denominamos la supervisión de la condición en máquinas”. Como en el caso de las personas, “en el de las máquinas también hay una serie de parámetros que son representativos de su salud, controlarlos te permite ahorrar costes, porque sólo intervienes las máquinas cuando empiezan a presentar problemas, y mejoras la disponibilidad”.
Su ponencia gira en todo a la colaboración de Dira Reliability con “una empresa grande con una serie de máquinas completamente críticas”, cuya parada “introducían una indisponibilidad muy grande no sólo en su planta, sino de todo un complejo grande con plantas aledañas”. Cada cuatro años, se programan intervenciones tras las cuales se vuelven a arrancar “y no pueden parar”. Hay que considerar que, cuando se programa una parada, “el resto de complejo se tiene que poner de acuerdo para intervenir también sus unidades”.
“Si se puede detectar un problema en una fase incipiente, quizás se pueda llevar a cabo una parada de corta duración, para intervenir y volver a arrancar”, apunta Rubén Ramírez. “Si no eres capaz de controlar esos parámetros, te encontrarás con la parada cuando menos lo esperas, sin tener preparados los repuestos ni los equipos de mantenimiento, y sin poder avisar a las plantas a las que suministras productos”.
El mantenimiento predictivo comienza en los años 50 y 60 en una serie de iniciativas conjuntas entre la industria aeronáutica y la armada norteamericana. “Se dieron cuenta de que había poca relación entre el mantenimiento tradicional, que programaba el cambio de un componente cada varios miles de horas, y la fiabilidad que conseguían”. La URSS se sumó a la carrera y en los años 70 “tenía siete laboratorios para analizar vibraciones en todas las máquinas”.
Los parámetros a controlar incluyen diferentes variables como la vibración, que ofrece información sobre el estado de máquinas rotatorias; las termografías, mapas de calor que se usan mucho en equipos eléctricos; o los ultrasonidos, para detectar los que generan las máquinas a partir los 30 kilohercios, imperceptibles para el oído humano. “Todo esto se recogía offline y se volcaba, pero hoy todo se hace en tiempo real, con sensores tipo PLC, sistemas de adquisición con alta frecuencia de muestreo y se registra en tiempo real los datos”.
El cliente que centra la ponencia del CEO de Dira Reliability cuenta con “cientos de máquinas rotatorias, pero cuatro supercríticas”. Su objetivo era extender las paradas programadas a seis años. “El departamento de IT pensó en desarrollar una serie de algoritmos en modelos de machine learning, basados en datos en tiempo real, para que avisaran ante cualquier anomalía”, explica.
En ese momento, aparece el problema complejo: “mantenimiento dice que a lo mejor no va a servir, porque no es tan sencillo escoger los datos a entrenar. Llegan a un consenso IT y mantenimiento para buscar una empresa pegamento entre los datos y el negocio que dijera si es posible o no resolver el problema; y ahí jugamos ese rol”, afirma Rubén Ramírez.
Dira Reliability puso a trabajar “a un equipo técnico multidisciplinar en el que estaban implicados responsables del proceso de producción del cliente, expertos del fabricante de la maquinaria, analistas de vibraciones, especialistas en fiabilidad dinámica y en la fiabilidad de instrumentación y control y especialistas en la metodología AMFE y FMEA, que es el análisis de los modos de fallo”.
Según Rubén Ramírez, “el fallo general no existe en la máquina, existen fallos puntuales que van dando consecuencias y provocan que fallen otras cosas”. Por eso, “hay que empezar a predecir los fallos más críticos y ahí es donde entra en juego la metodología de los análisis de modo de fallo”. Su aproximación parte, por consiguiente, de analizar los fallos, identificar los más críticos y reunir las variables con más peso en ellos, el histórico disponible y el número de eventos similares. Todo ello debe servir para entrenar los modelos.
Como guía para la actividad de supervisión de condición, se elabora una matriz de criticidad: a cada elemento se asocian elementos como los fallos potenciales que puede tener y la frecuencia. “Una vez enumerados los modos de fallo, clasificados los más críticos y analizadas las variables de interés para cada uno de ellos, hay que ver si tenemos esas variables disponibles y desde cuándo”, señala Rubén Ramírez.
Para generar un buen dataset necesitamos variables disponibles y eventos. En algún caso, los datos sólo se vienen generando desde hace dos años. ¿Son suficientes para entrenar modelos? “Depende, son máquinas que no están fallando constantemente, no hay eventos suficientes para poder entrenar. Sé que estoy rebajando el suflé de la inteligencia artificial, pero es la realidad: si no tenemos datos y eventos a lo mejor no se puede hacer todo”.
De todos los modelos de fallo identificados, sólo el 6% eran graves y el 10% moderados. “Sólo ese 16% tiene retorno de la inversión, el resto no porque apenas tienen incidencia en la producción”, explica el CEO de Dira Reliability. Además, “no todas las variables de interés están disponibles en la misma franja temporal, y eso imposibilita tener información de todos los modos de fallo a la vez y poder entrenar”.
Finalmente, el plan de acción incluye establecer un procedimiento adecuado para etiquetar eventos de interés; e instalar instrumentación supervisora para mejorar el seguimiento de variables de interés que no estuvieran disponibles, “hay sensores que permiten analizar el aceite en tiempo real”.
“En algunas ocasiones, es necesario rebajar las expectativas sobre los sistemas basados en IA, no por carencias de la tecnología, sino por la falta de datos y eventos suficientes con los que entrenar los modelos”, afirma Rubén Ramírez como conclusión. “Por esta misma razón, los sistemas clásicos de alarma o de soporte a la decisión (SSD), basados en reglas lógicas, son todavía más eficientes. Hasta que no tengamos preparado nuestro sistema con buenas variables de interés y etiquetando esos eventos para el futuro, esos sistemas clásicos serán todavía más eficientes”.