
La industria siderúrgica repiensa su cadena de suministro a golpe de código y apuesta por un acero verde libre de fósiles
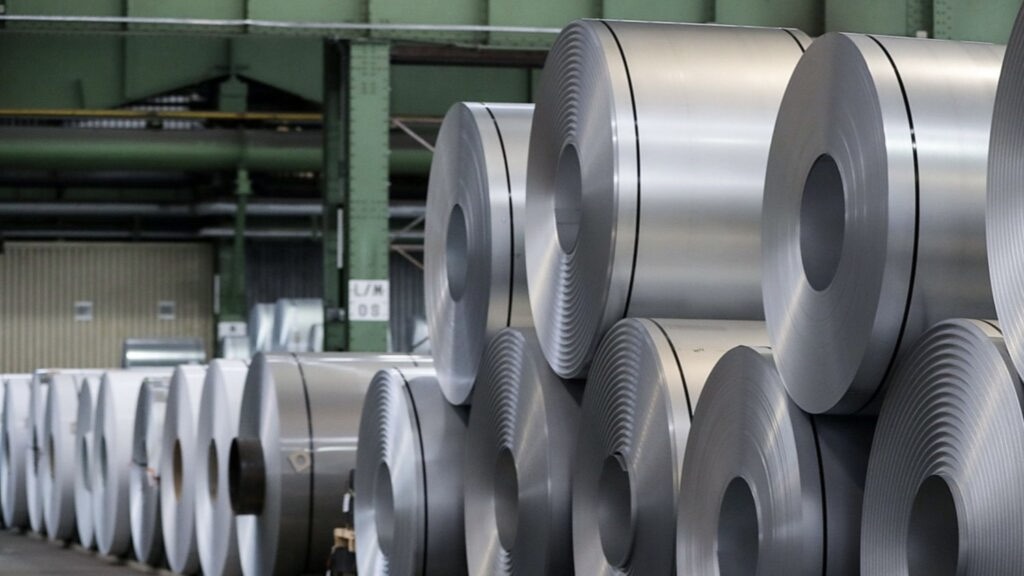
El acero, columna vertebral de la civilización industrial, está iniciando su transformación más profunda desde finales del siglo XIX. Responsable de más del 7% de las emisiones mundiales de CO2 al año, la industria siderúrgica se consolida como una de las más contaminantes del plantea. Por ello, un cambio hacia una producción sostenible es un imperativo climático que no admite dilaciones. Para 2030, según la Agencia Internacional de la Energía (IEA), deberían producirse al menos 100 millones de toneladas anuales de acero con emisiones casi nulas para mantenerse dentro de los márgenes del Acuerdo de París, pero los proyectos anunciados apenas alcanzan una décima parte. En este marco, la inteligencia artificial (IA) y los gemelos digitales pueden ser los nuevos ingenieros capaces de diseñar, controlar y escalar procesos más eficientes y limpios.
La reinvención del sector pasa por propuestas sostenibles, la vía más eficiente para las empresas. Ejemplo de ello es el consorcio europeo DiGreeS, que ha desarrollado un sistema de clasificación inteligente de chatarra basado en láseres y algoritmos de IA, complementado por un gemelo digital del flujo de materiales reciclado. De hecho, cada vez más clientes, especialmente en sectores como la automoción, exigen una certificación precisa de la huella de carbono del acero que compran, por lo que estos gemelos abarcan no solo el proceso de fundición, sino toda la cadena de suministro.
En Alemania, thyssenkrupp Steel ha instalado un “Central Operation Cockpit” que permite a un solo operador supervisar toda una línea de producción mediante asistentes de IA, predicciones energéticas y mantenimiento preventivo. Este avance, además de hacer un seguimiento como el de DiGreeS, incrementa la productividad y reduce el consumo energético sin necesidad de ampliaciones físicas. Mientras tanto, Tata Steel India ha desplegado más de 550 modelos de IA en toda su cadena de valor, desde la gestión de hornos hasta la optimización de rutas logísticas internas, que demuestra que la digitalización aplicada de forma integral puede recortar emisiones al tiempo que mejora márgenes y eficiencia.
Más allá de la cadena
Además de la optimización de la cadena de suministro, la brasileña Gerdau colabora con Fero Labs para aplicar IA en la optimización del propio acero, lo que ha supuesto ahorros de tres dólares por tonelada de acero producido y una reducción de emisiones exponencial. A medida que estas soluciones se validan a escala industrial, se configura una nueva lógica de funcionamiento: las acerías del siglo XXI serán fábricas cognitivas, donde los datos fluyen y las decisiones se toman en tiempo real gracias a modelos de simulación que integran IA, sensores, gemelos digitales y plataformas industriales como Siemens Xcelerator.
El reto, sin embargo, no es menor. Las inversiones necesarias para sustituir hornos tradicionales por nuevas tecnologías superan en muchos casos el 50 % los los gastos de capital habituales en las empresas. La disponibilidad y coste del hidrógeno verde, la capacidad de acceso a renovables baratas, el déficit de profesionales híbridos que combinen conocimientos en metalurgia y análisis de datos son barreras que limitan el ritmo de adopción. Sin embargo, las palancas se multiplican, desde los bonos verdes vinculados a acero limpio, hasta la aparición de ecosistemas digitales-industriales que permiten reducir el coste de implementación mediante modelos virtuales escalables.
Nuevas invenciones
El concepto de acero verde engloba múltiples rutas tecnológicas que comparten un objetivo común: eliminar el carbono fósil del sector siderúrgico. Entre las más prometedoras destaca el empleo de hornos eléctricos alimentados con energías renovables de plantaciones cercanas. Este es el tapete sobre el que trabaja H2 Green Steel, una empresa sueca que está construyendo en la ciudad de Boden la primera planta de producción masiva de acero libre de fósiles, verdaderamente pionera mundial en las cero emisiones. Además, tiene el apoyo de una financiación de 4.200 millones de euros y un diseño completamente virtualizado en gemelo digital.
En paralelo, proyectos como HYBRIT han comenzado a almacenar hidrógeno verde en cavidades subterráneas monitorizadas con gemelos operacionales, que sustituyen a los combustibles fósiles. Esta innovación, impulsada por SSAB, LKAB y Vattenfall, podría reducir en un 40 % los costes variables de suministro de hidrógeno, actualmente uno de los mayores cuellos de botella de la industria.
El próximo lustro será decisivo. Para 2026 está previsto que arranque la producción comercial en la planta de H2 Green Steel, y, en 2027, Tata Steel India espera dejar atrás el alto horno con ayuda del gemelo digital. Si estas iniciativas logran alcanzar los niveles de eficiencia, reducción de emisiones y calidad industrial esperados, podrían marcar el punto de inflexión hacia una nueva era del acero.