
Gemelos digitales para el control marítimo, impresión 3D basada en materiales reciclados y monitorización de la calidad de materiales
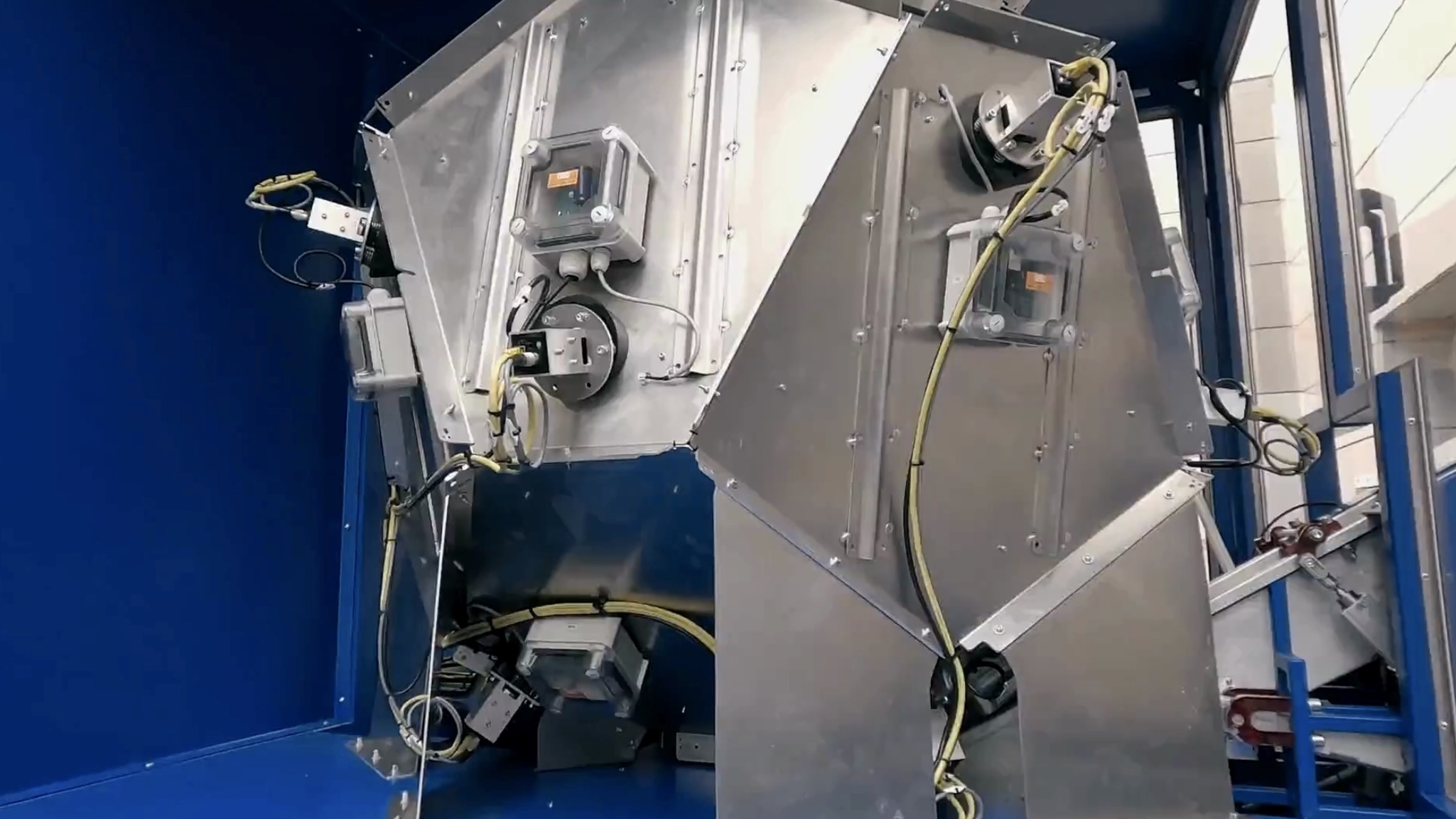
En un panorama empresarial en constante cambio, las soluciones tecnológicas innovadoras se han convertido en el núcleo de la transformación en múltiples sectores. Desde la sostenibilidad en la manufactura hasta la automatización en la logística, las empresas están adoptando nuevas tecnologías para enfrentar desafíos específicos y optimizar sus operaciones. A continuación, exploramos cuatro casos de éxito recientes donde la adopción de soluciones tecnológicas ha permitido a las empresas del ecosistema Atlas superar obstáculos, impulsar su competitividad y eficiencia.
EOLOS Floating Lidar Solutions, una empresa de vanguardia en el monitoreo marino, se une con Ibernova para elevar su sistema de gestión de boyas de alta tecnología. La empresa necesitaba obtener un control detallado de cada una de sus boyas y sus componentes en tiempo real, además de mejorar la eficiencia en sus operaciones y el mantenimiento de entornos hostiles. Además, se requería organizar la documentación, evitar duplicidades en archivos de diseño y optimizar la coordinación del equipo para evitar retrabajos. Ibernova propuso la plataforma 3DEXPERIENCE, que permite a EOLOS crear gemelos digitales de cada boya y gestionar exhaustivamente los más de 8000 componentes de cada una. Con la herramienta, EOLOS obtiene listas completas, producción y mantenimiento directamente desde la plataforma, optimiza su documentación y puede buscar y filtrar productos con mayor eficiencia.
Por su parte, Synersight destaca por su solución para la automatización de procesos logísticos mediante la actualización de sus AGVs (vehículos de guiado automático). Uno de sus clientes enfrentaba limitaciones para producir, debido a las restricciones en las funcionalidades de los medios existentes, lo cual exigía una mejora en el rendimiento y la flexibilidad operativa de los AGVs antiguos. La actualización no solo aumentó el número de destinos disponibles, sino que también introdujo mejoras en la carga online, la recopilación de datos y la capacidad de diagnostico remoto. Con una serie de innovaciones, como la detección de defectos en tiempo real y el monitoreo de condiciones ambientales, el cliente ya puede operar con un sistema más robusto, intuitivo y confiable.
Soluciones para la sostenibilidad
IDIONAL ha hecho de su planta el eje de una economía circular. El centro tecnológico ha dado un paso hacia la sostenibilidad en la industria manufacturera a través de su tecnología de impresión 3D que utiliza materiales reciclados como materia prima. Para transformar los residuos en piezas personalizadas en la propia planta, la impresora emplea plásticos reciclados de PET y policarbonatos de alta resistencia. Su implementación ha demostrado ser efectiva en muchos sectores industriales, incluida la logística, y las oportunidades que ofrece aprovechar sus residuos. El objetivo no es solamente es reducir el impacto ambiental sin comprometer la calidad de los productos, sino que también se han reducido costes, disminuido la dependencia de proveedores externos y encontrado una ventaja competitiva en sectores como la automoción y los bienes de consumo.
El Instituto Tecnológico de Informática (ITI) ha revolucionado el reciclaje de polipropileno, material empleado en los salpicaderos de coches, en la multinacional Tier-1, perteneciente al sector automotriz. El desafío residía en cumplir con los estrictos estándares de pureza exigidos por los fabricantes, para lo cual era necesario garantizar que el material reciclado estuviera libre de contaminantes. ITI desarrolló una solución única basada en su tecnología ZG3D, integrada con un sistema de 9 cámaras y una iluminación específica, y que permite monitorear en tiempo real la calidad del material reciclado y controlar contaminaciones durante el proceso de fabricación. El éxito de este proyecto no solo se traduce en la recuperación de materia prima por valor de 500.000 euros anuales, pues el polipropileno es un material de coste elevado, sino en la capacidad de la empresa para reciclar el material de acuerdo con las especificaciones de los fabricantes. Esta tecnología ha permitido al cliente optimizar recursos y reducir costes, mientras cumple con los estándares de calidad.