
Digitalización a pie de fábrica con escaneado forestal, flotas aéreas autónomas y visión artificial en el ecosistema Atlas
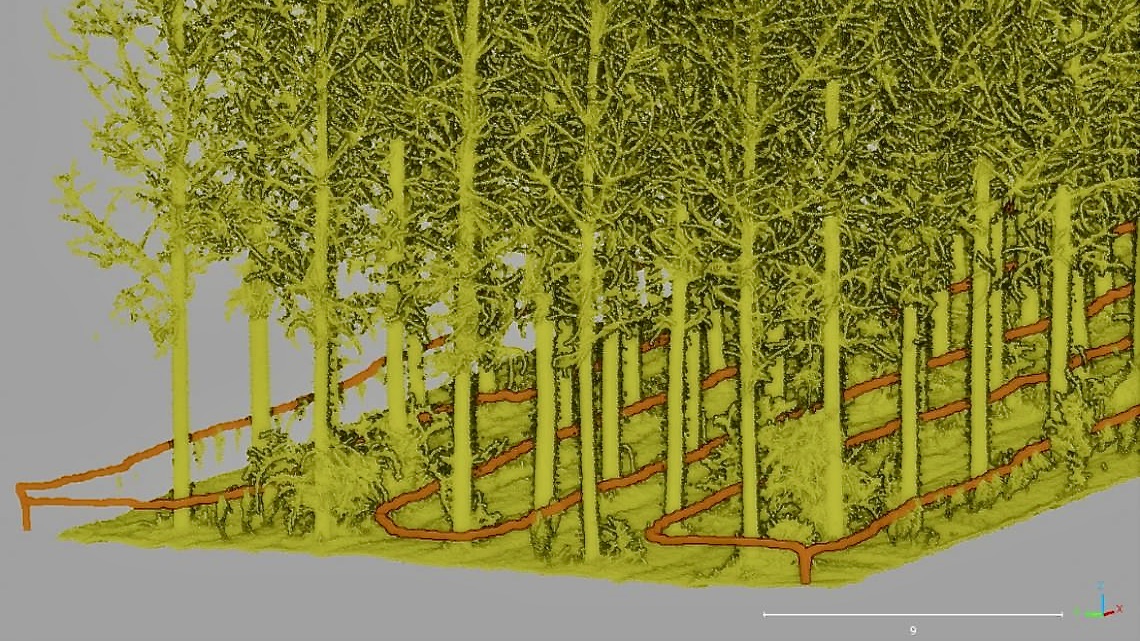
En el ecosistema Atlas Tecnológico, empresas de sectores tan dispares como la construcción metálica, la madera estructural o la ingeniería aeroespacial están desplegando proyectos que digitalizan tareas críticas, multiplican la velocidad operativa y elevan la toma de decisiones a tiempo real. Gracias a configuradores 3D, sensores láser y gemelos digitales, estas iniciativas reducen plazos de semanas a minutos, liberan talento técnico para la innovación y preparan a la industria para los desafíos de la próxima década.
El suministro responsable de madera exige conocer con precisión cada metro cúbico disponible. Garnica se apoyó en la Universidad de León y su hub digital DIGIS3 para saltar del inventario manual a la captura masiva de datos con escáner láser móvil (LiDAR); esta es una tecnología de teledetección que utiliza pulsos de luz para medir distancias y crear modelos 3D precisos de un entorno. El proyecto ha arrancado con un taller intensivo de ocho horas abierto a operarios y mandos intermedios, para, posteriormente, comenzar una prueba de concepto en montes de Valencia de Don Juan y, finalmente, culminar con la adquisición del sistema y la contratación de un geoinformático formado en la propia ULE.
El nuevo flujo convierte en minutos lo que antes requería jornadas de medición. El LiDAR barre la parcela y un software de nube de puntos calcula volumen, especie y diámetro medio por árbol con una precisión subcentimétrica. Los datos alimentan un dashboard que ajusta los planes de tala al crecimiento real. Además, el grupo de investigación y Garnica negocian la patente de algoritmos propios de clasificación, con vistas a escalar la solución a la gestión de inventarios industriales de tableros y chapas.
En el marco del Programa Misiones 2024, CT Ingenieros lidera el Proyecto Gavilanso junto a sus socios IDNEO, ATYGES e IDBOTIC, con el objetivo de dar respuesta a tres de los grandes retos que plantea la Movilidad Aérea Urbana: la autonomía, la seguridad y la coordinación de flota. Para ello, el consorcio ha desarrollado una batería modular de alta densidad, gestionada por un sistema inalámbrico configurable por software, que permite adaptarse a distintas necesidades operativas. Además, el proyecto refuerza la ciberseguridad de los sistemas embarcados y diseña un sistema de gestión de flotas basado en inteligencia artificial (IA), capaz de coordinar vehículos en «enjambre», asignar rutas y optimizar las cargas en tiempo real.
La raíz tecnológica del proyecto es un Centro de Misión Virtual que permite simular las misiones urbanas antes de que los vehículos despeguen. Para ello, se utiliza un gemelo digital del sistema de baterías junto con simulaciones Hardware-in-the-Loop, una técnica usada para el desarrollo y comprobación de sistemas embebidos en tiempo real. Esta combinación permite afinar el consumo energético, anticipar posibles fallos y planificar el mantenimiento de forma predictiva sin necesidad de poner en riesgo los equipos reales. El gemelo está conectado tanto con torres U-space como con sistemas convencionales de control de tráfico aéreo, lo cual permite validar la convivencia segura entre vehículos aéreos eléctricos (eVTOL), drones logísticos y la aviación tradicional. El objetivo, para CT Ingenieros, es claro: reducir al menos un 15% el consumo energético por kilómetro y minimizar los incidentes durante las pruebas de integración previstas para 2026.
Por otra parte, y en línea con la carrera de la industria por eliminar errores y aumentar la trazabilidad, Tupl ha presentado su proyecto “Automated Defect Detection for Manufacturing”. La iniciativa aborda el punto más sensible del control de calidad: detectar microfisuras, faltas de soldadura o componentes ausentes sin ralentizar la línea. Basada en la plataforma TuplOS, la solución combina cámaras de ultra‑alta resolución con un entorno no‑code MLOps que permite a los propios ingenieros de planta etiquetar imágenes, entrenar modelos y desplegarlos en cuestión de horas. El sistema aprende sobre la marcha, añade nuevas clases de defecto y se integra con el MES de fábrica para enviar alertas en tiempo real, de modo que la operativa no necesita detenerse ni para actualizar algoritmos.
El centro de gravedad sobre el que se apoya el proyecto es una arquitectura híbrida edge‑cloud. Es decir, las imágenes se procesan primero en el borde para cumplir los tiempos de ciclo, mientras que la nube hospeda el reentrenamiento continuo de los modelos. De este modo, la IA devuelve la inferencia al PLC en milisegundos y ajusta automáticamente los parámetros de máquina o desvía las piezas sospechosas a una vía de reproceso. En apenas tres meses de producción, el piloto ha recortado en 40 % los defectos no detectados, elevado el throughput un 20 % y ahorrado más de 750. 000 dólares anuales en reprocesos y garantías, al tiempo que libera a los operarios de tareas de inspección repetitiva para concentrarse en análisis de causa raíz y mejoras de proceso.