
Así desarrollan las fábricas sus propios “ojos” con visión artificial para reinventar la industria 4.0
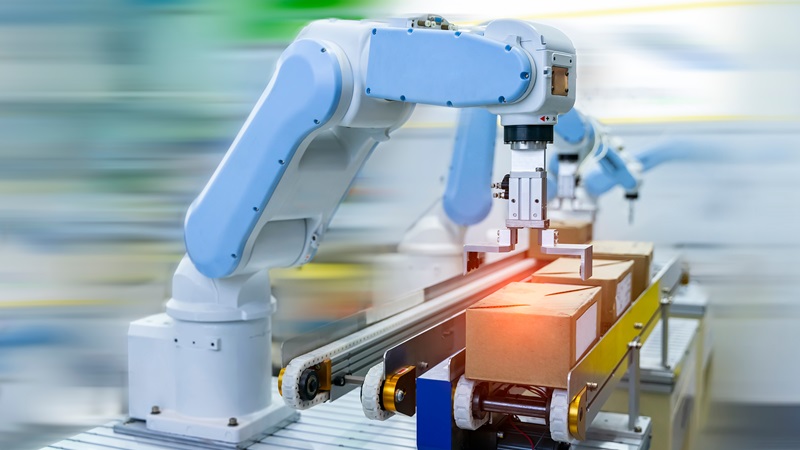
En el umbral de la industria 4.0, la visión artificial (VA) ha evolucionado hasta convertirse en el núcleo de procesos inteligentes, colaborativos y seguros. La VA, rama de la inteligencia artificial (IA), extrae información de imágenes digitales, vídeos y otras entradas visuales a través del aprendizaje automático (ML). Es decir, dota a las máquinas de una “vista” capaz de interpretar y reaccionar ante su entorno. De este modo, elementos tan dispares como sensores neuromórficos que reaccionan en microsegundos y plataformas inmersivas de realidad virtual (VR) para formación, están ya redefiniendo la forma de operar en las fábricas. Este tipo de recursos podrían reducir el volumen de datos procesados y garantizar la trazabilidad de cada inspección o decisión automatizada, pero, pese a su potencial, son tendencias aún poco explotadas en España. Para acelerar su adopción, centros tecnológicos como Cartif acompañan a pymes de automoción y agroindustria en pilotos de inspección óptica.
Los sensores neuromórficos, o, en sí, la ingeniería neuromórfica, son unos sistemas que, mediante circuitos analógicos, imitan ciertos funcionamientos del sistema nervioso humano. Los aplicados a la VA, también conocidos omo Dynamic Visión Sensors (DVS), son una especie de «ojos» que, ante los cambios del entorno, pueden reaccionar al instante sin desperdiciar ingentes volúmenes de datos. Esta tecnología, inspirada propiamente en la retina humana, en lugar de capturar imágenes completas del estado de la fábrica, solamente registran los cambios en la luminancia de cada pixel. La innovación permite a las fábricas «ver» y actuar más velozmente, lo que se traduce, entre otras cosas, en un ahorro de hasta el 90% en el procesamiento de datos.
Para el sector de la automoción y la electrónica, los DVS suponen un salto cualitativo. En líneas donde el tiempo es una variable clave, estos sensores detectan fisuras en soldaduras o partículas errantes a velocidades superiores a un metro por segundo. Así, se frena la cadena solo cuando verdaderamente es necesario. El resultado, según el Instituto de Microelectrónica de Sevilla (IMSE-CNM), es una reducción de hasta el 30 % en piezas rechazadas y un consumo energético sensiblemente menor que con cámaras tradicionales. Un caso de uso que demuestra la eficiencia de esta practica es el protagonizado por Hinojosa Packaging Group, que ha comenzado a aplicarlos par a la inspección de envases en cartón reciclado.
Otra de las apuestas de la VA para optimizar la producción es el few-shot learning. Hasta ahora, los proyectos de visión artificial se topaban con el gran escollo de necesitar miles de imágenes anotadas para funcionar con fiabilidad. Con el aprendizaje few-shot, basta con ofrecer al algoritmo entre cinco y diez ejemplos seleccionados de la pieza o defecto que se quiere detectar. Con este nuevo enfoque, se puede recortar hasta un 85% del tiempo dedicado para preparar y etiquetar datos . En la práctica, esto significa que un fabricante puede adaptar su sistema de inspección a un nuevo componente en apenas unos días, en lugar de retrasar su lanzamiento semanas o meses.
Optimizar mundos virtuales
Los gemelos digitales vivos llevan la fábrica al plano virtual en tiempo real. Al combinar las imágenes 2D y 3D capturadas por cámaras de visión artificial con motores de simulación se crea un “clon” digital de toda la línea de producción. Sobre este reflejo virtual se pueden ensayar nuevos procesos, redistribuir máquinas o probar diferentes flujos de trabajo sin necesidad de detener ni un solo minuto la planta física. Además, al trabajar con datos reales (velocidades de cinta, tiempos de ciclo o tasas de rechazo), estos gemelos predicen con antelación posibles cuellos de botella y permiten afinar la eficiencia antes de invertir en cambios costosos. Empresas como Siemens implementa gemelos digitales en la planta de Amberg (Alemania), donde más del 75 % de los ensayos de reconfiguración se realizan de forma virtual. Esto ha permitido reducir costes de diseño en un 30 % y acortar los tiempos de instalación en un 25 %.En España, por ejemplo, GMV realiza integraciones similares en líneas aeroespaciales.
Por su parte, la visión artificial impulsa la formación de operarios mediante realidad virtual y aumentada (AR), por lo que el reskilling se transforma en una experiencia inmersiva y guiada. Gracias a gafas AR, capaces de identificar la posición de manos y herramientas, los trabajadores reciben instrucciones superpuestas directamente en su campo visual, mientras los simuladores VR reproducen con detalle cada estación de la línea. Antes de afrontar una tarea real, el sistema corrige gestos, alerta sobre pasos omitidos y evalúa la postura en tiempo real, lo que reduce en un 40 % el tiempo necesario para adquirir competencias. Dentro de nuestro hub, la plataforma Onirix replica estas experiencias y, paralelamente, reporta incrementos de productividad del 30 % en mantenimiento, mientras el integrador Synersight añade rutas de AGV virtuales para practicar operaciones sin riesgo.