
Antonio Conesa muestra en ‘La Hora Premium’ soluciones de mantenimiento predictivo que aseguran el ahorro de costes y la sostenibilidad
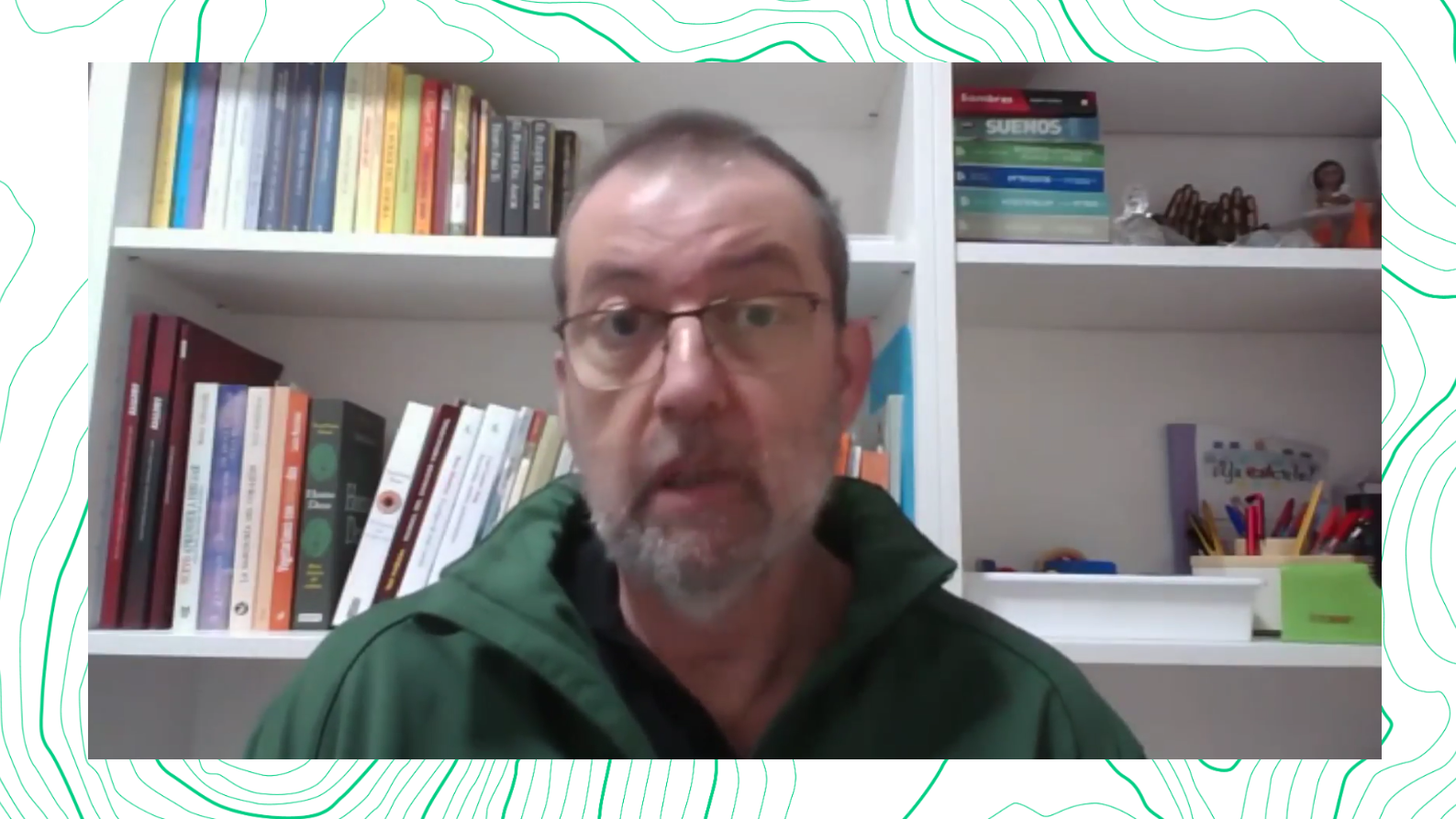
Antonio José Conesa, responsable de Departamento Técnico de Henkel Ibérica, ha participado en ‘La Hora Premium’ con una ponencia titulada ‘Soluciones de mantenimiento 4.0 que aumentan la fiabilidad en las instalaciones industriales’, moderada por Pablo Oliete, que se inserta en el ciclo temático sobre mantenimiento predictivo. Tras la primera ponencia, protagonizada por Rubén Ramírez (Dira Reliability), en la que expuso los orígenes y claves del éxito de esta metodología, Conesa ha ido a lo concreto en su intervención exponiendo diversas soluciones IIOT de Loctite que permiten “detectar indicios de fallos antes de que ocurran y establecer tendencias, gracias a un monitorizado continuo y un tratamiento de datos mediante IA”. “Con estas soluciones vamos a evitar paradas no programadas, que pueden ocasionar enormes costes, vamos a contribuir a la sostenibilidad por el control de fugas, y a mantener la seguridad de las personas”, ha añadido.
Conesa ha comenzado su exposición estableciendo la diferencia entre un mantenimiento reactivo, que se produce cuando ocurre el fallo, y el mantenimiento predictivo, en el que se prevé el fallo antes de que ocurra. Además, ha ido un paso más allá, hablando sobre mantenimiento prescriptivo, que es aquel que, además, recomienda acciones específicas para mitigar riesgos y optimizar el rendimiento de los activos.
Soluciones inteligentes
El experto ha comenzado explicando la solución de bridas inteligentes desarrollada por el grupo. “Hay industrias, como la química o petroquímica, en las que las consecuencias de una fuga pueden ser muy críticas, y es ahí donde resulta muy conveniente intervenir y monitorizar”. Esas consecuencias de fugas pueden ser de tipo ambiental o que afecten a la seguridad de las personas. También, pueden darse en zonas con poca accesibilidad o baja frecuencia de inspección.
Esta brida funciona con un sensor que recopila datos confinado en el hueco de la brida, que es sellada mediante cinta de silicona o con un composite. Esos datos son trasladados a un dispositivo periférico, capaz de recibir la información de ocho bridas, que está conectado a la nube, donde se produce el análisis de los datos. Por último, la información se visualiza a través de una app. “El sensor detectaría cualquier fuga y haría saltar una alarma en el teléfono móvil, de modo que tengo capacidad de ir a verlo y planificar la reparación antes de que se dé el fallo”, explica Conesa. Esta solución se puede aplicar también en tuberías, interior de envolventes o bajo aislamientos. “Los ahorros acaban siendo enormes, principalmente por la posibilidad de programar las reparaciones”.
El experto ha compartido también la solución de la compañía de purgadores inteligentes de vapor. “Las líneas de vapor tienen una serie de problemas relacionados con la condensación de agua y los golpes de ariste, para lo cual se instalan purgadores de vapor, que pueden presentar complicaciones: que se queden abiertos y se dé una fuga constante de vapor, con la consecuente pérdida económica y emisiones descontroladas de CO2; o que se queden cerrados, lo que supone problemas de condensado y de pérdida de eficiencia y calidad en la producción”, ha explicado. Además, la inspección manual de estos purgadores requiere mucha mano de obra y se da un retraso entre en fallo y la detección, dependiendo de la periodicidad de la inspección.
Su solución inteligente recopila datos para un control continuo de los purgadores. Mediante la monitorización continua de la temperatura de entrada y de salida al purgador, junto a un análisis de datos basado en IA para detectar cualquier tipo de problema de funcionamiento y establecer tendencias, se consigue una detección inmediata de problemas. “Son cuestiones que con una inspección visual o manual no se puede hacer”, asegura.
Por último, Conesa ha hablado sobre los equipos rotativos inteligentes. Están pensados para proteger activos críticos en bombas centrífugas, motores eléctricos, cajas de engranajes, ventiladores y turbinas, o decantadores centrífugos, entre otros. “Son sensores que se integran en la máquina y que permiten monitorizar los equipos para reaccionar a los problemas y evitar reparaciones de urgencia”, ha explicado.
Estos equipos inteligentes transmiten información sobre seis parámetros: vibración triaxial (aporta información direccional de las vibraciones del equipo), señales de ultrasonidos (“el primer síntoma de un problema”), temperatura (calentamiento por fricción o mal funcionamiento), humedad (para asegurar la integridad del sensor), velocidad de rotación del equipo y flujo magnético. “Son seis sensores en uno, que permiten la detección de fallos de forma instantánea”, ha asegurado Conesa.
“Se trata de soluciones no intrusivas, que se instalan y se comienzan a usar y a obtener información, y que al almacenarse en la nube tampoco requieren de ningún software específico”, ha explicado. “Son sistemas totalmente inalámbricos, que no necesitan gateways ni cuadros periféricos adicionales”.
“Contra más grandes son los equipos, más interesante es su monitorización, puesto que la reposición no es tan sencilla”, ha asegurado. “Industrias químicas y petroquímicas, y otras manufactureras, como la industria papelera, han introducido ya estas soluciones con éxito”, ha concluido.
Tras la ponencia de Rubén Ramírez y de Antonio José Conesa, en el ciclo participará también Ángel García Bombín, Industrial Digital Transformation Director en Sonae Arauco, quien ofrecerá la ponencia ‘Uso de sistema PdM integrado en la organización’. El ciclo finalizará con una mesa redonda titulada ‘Diferentes perspectivas del mantenimiento predictivo’, en la que participarán Beltrán Blázquez (Cofundador y CEO en Synnect), Borja López (HO Industrial Means Maintenance WLCA350 en Airbus), Román Martín (COO & KAM en LIS Data Solutions) y Xavier Riba (Cofundador y Sales Manager en Innovae y colaborador en Atlas Tecnológico).