
Ángel García Bombín incide en la Hora Premium en la importancia de pasar de las alarmas a las acciones en el mantenimiento predictivo
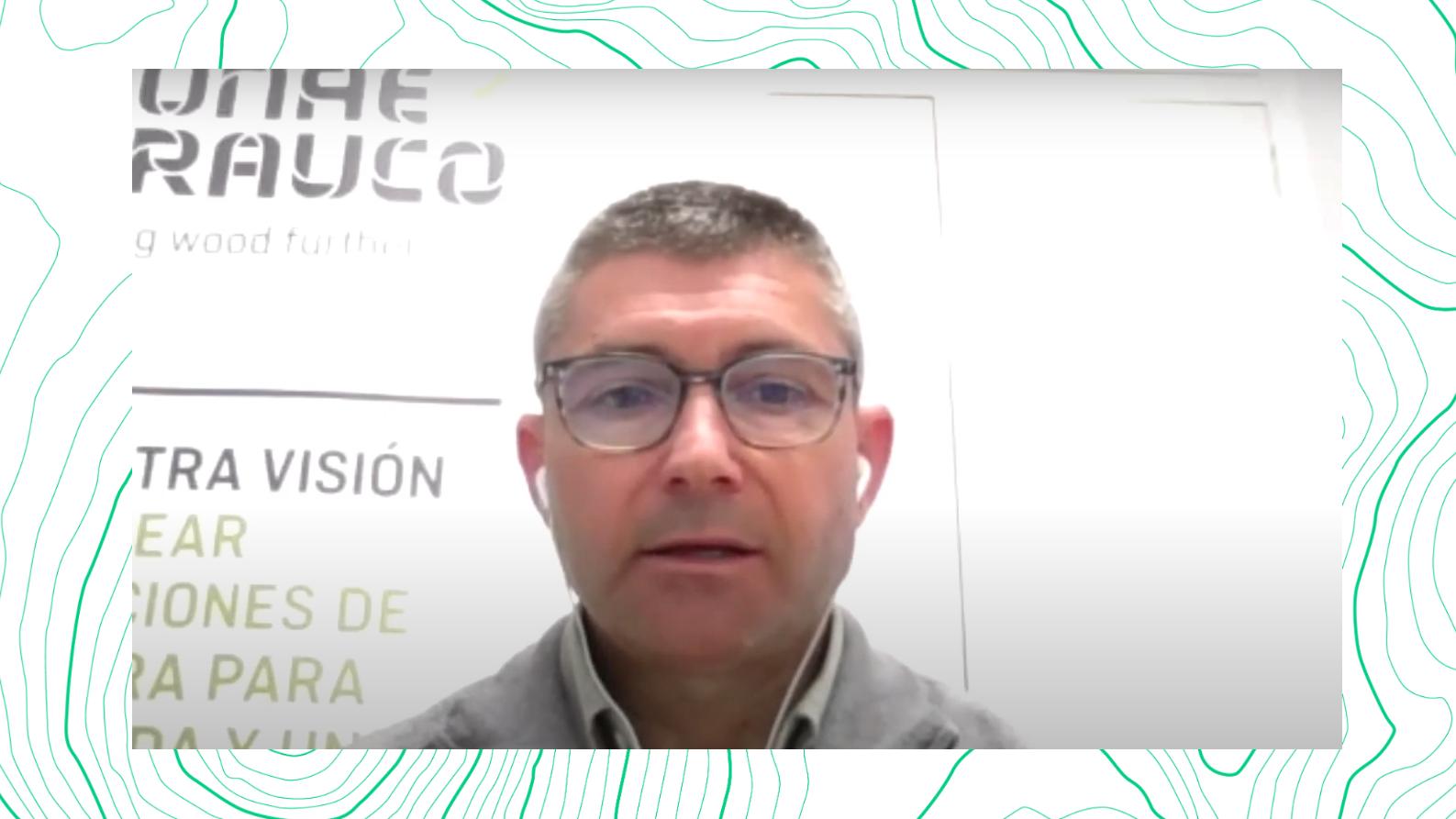
Ángel García Bombín, director de Transformación Digital de Sonae Arauco, ha participado en ‘La Hora Premium’ con una ponencia titulada ‘Uso de sistema PdM integrado en la organización’, moderada por Pablo Oliete, que se inserta en el ciclo temático sobre mantenimiento predictivo. Tras las ponencias de Rubén Ramírez (Dira Reliability y Antonio José Conesa (Henkel Ibérica), García Bombín ha expuesto el caso práctico de Sonae Arauco en la integración de un sistema de mantenimiento predictivo común para todas sus plantas productivas (la compañía está presente en nueve países), y ha destacado que el éxito del sistema está en la capacidad de unir las alarmas con las acciones: “saber qué hacer y cuándo hacerlo es la parte más difícil”. “Se requiere formación y personas específicas dedicadas a manejar la herramienta”, ha declarado.
El experto ha comenzado con una introducción sobre Sonae Arauco, uno de los mayores actores mundiales en soluciones sostenibles a base de madera: mobiliario, interiorismo y construcción. La compañía se caracteriza por su impulso de la industria 4.0, con fábricas en tiempo real e integración del machine learning y la IA. “Vinculamos los esfuerzos de digitalización con los objetivos estratégicos, asegurándonos de que todos los recursos, capacidades y habilidades se asignen de manera adecuada”, ha explicado. En este sentido, ha destacado la colaboración como pilar fundamental para fomentar la cooperación entre diferentes departamentos, equipos y socios, así como para evitar duplicidades.
Como punto fundamental hacia la digitalización, García Bombín ha señalado la necesidad de unir el edge con la nube. “Lo que tenemos en la planta es lo que tiene que ver con el tiempo real y la alarmística, y esto se complementa con la analítica y el entrenamiento de modelos con IA, que está en la nube”. Además, ha señalado la importancia de tener una buena gobernanza y de utilizar una cultura Dev/Ops en el desarrollo de software, fundamental para tener “sistemas que mejoran con el tiempo”.
A este camino hacia la digitalización se le une un alineamiento estratégico. “Queremos una plataforma global, común para todas las plantas del grupo, y esto es de las cosas que más cuestan”, ha explicado. “Pero poco a poco ves las ventajas: puedo comprobar cualquier elemento en cualquier fábrica, y eso es esencial”.
Sobre la aplicación del sistema de mantenimiento en la compañía, García Bombín ha asegurado que la creación de áreas de fiabilidad fue la clave. “Según nuestra experiencia, los departamentos de mantenimiento no tienen los conocimientos necesarios para sacar el máximo rendimiento al sistema de mantenimiento predictivo, ya que está más acostumbrado a ejecutar”, ha asegurado. La compañía ha creado departamentos de fiabilidad que son los encargados de dirigir y controlar el mantenimiento predictivo. “Estas personas necesitan formación en análisis de vibraciones; hasta que no la tienen, se tiene que suplir con el servicio ofrecido por el suministrador del sistema, que es fundamental que tenga un background industrial”.
En este punto, el experto ha destacado que lo más importante del sistema de mantenimiento predictivo es pasar de las alarmas a las acciones. “La mayor dificultad es cuando hay muchos sensores que generan alarmas: se debe saber qué hacer y cuándo hacerlo”, ha explicado. Esto es el mantenimiento prescriptivo. “Nuestro suministrador, que tiene acceso a la plataforma, va a recibir la alarma y va a incluir un nivel más de análisis: nos va a remitir una notificación, que une la alarma con las acciones a acometer”. “En los sistemas de mantenimiento predictivo hay un vacío entre la alarma y la acción, que lo tenemos que suplir con conocimiento interno o con conocimiento del proveedor, y esto es básico para sacarle todo el partido”.
García Bombín ha compartido el funcionamiento del sistema de mantenimiento predictivo de Sonae Arauco, basado sobre todo en sensores de rodamiento de vibraciones. “Mediante salida dinámica, con la forma de onda obtenemos el espectro de frecuencia y vemos qué tipo de error puede ser”, ha detallado. Para la colocación de los sensores, la compañía se ha basado en un estudio para definir la criticidad de cada máquina. “Hemos ido, sobre todo, a los equipos súper críticos”.
El experto ha explicado diversos casos concretos, como el de una alarma de desequilibrio en un secadero de la planta de Sudáfrica. “Nos saltó la recomendación de chequear la limpieza del rodete o de equilibrar si era necesario; se comprobó, se limpió y ni hizo falta equilibrar. Una simple tarea de limpieza que, si no se hubiera hecho, sí que habría deteriorado todos los demás puntos de la máquina”. “Este tipo de acciones van a aumentar la fiabilidad y la vida y disponibilidad de las líneas de producción”, ha añadido.
“Se debe trabajar sobre lo que te va a generar un problema y preverlo, para poder convertir una avería en una parada programada”, ha asegurado Ángel García Bombín. «El mantenimiento predictivo es una de las aplicaciones estrella dentro de la industria 4.0».
Tras la ponencia de Rubén Ramírez , Antonio José Conesa y Ángel García Bombín, el ciclo finalizará con una mesa redonda titulada ‘Diferentes perspectivas del mantenimiento predictivo’, en la que participarán Beltrán Blázquez (Cofundador y CEO en Synnect), Borja López (HO Industrial Means Maintenance WLCA350 en Airbus), Román Martín (COO & KAM en LIS Data Solutions) y Xavier Riba (Cofundador y Sales Manager en Innovae y colaborador en Atlas Tecnológico).