
Tratamiento virtual de semillas, menos de un segundo de latencia en aeronáutica y anticipar la demanda de jamón
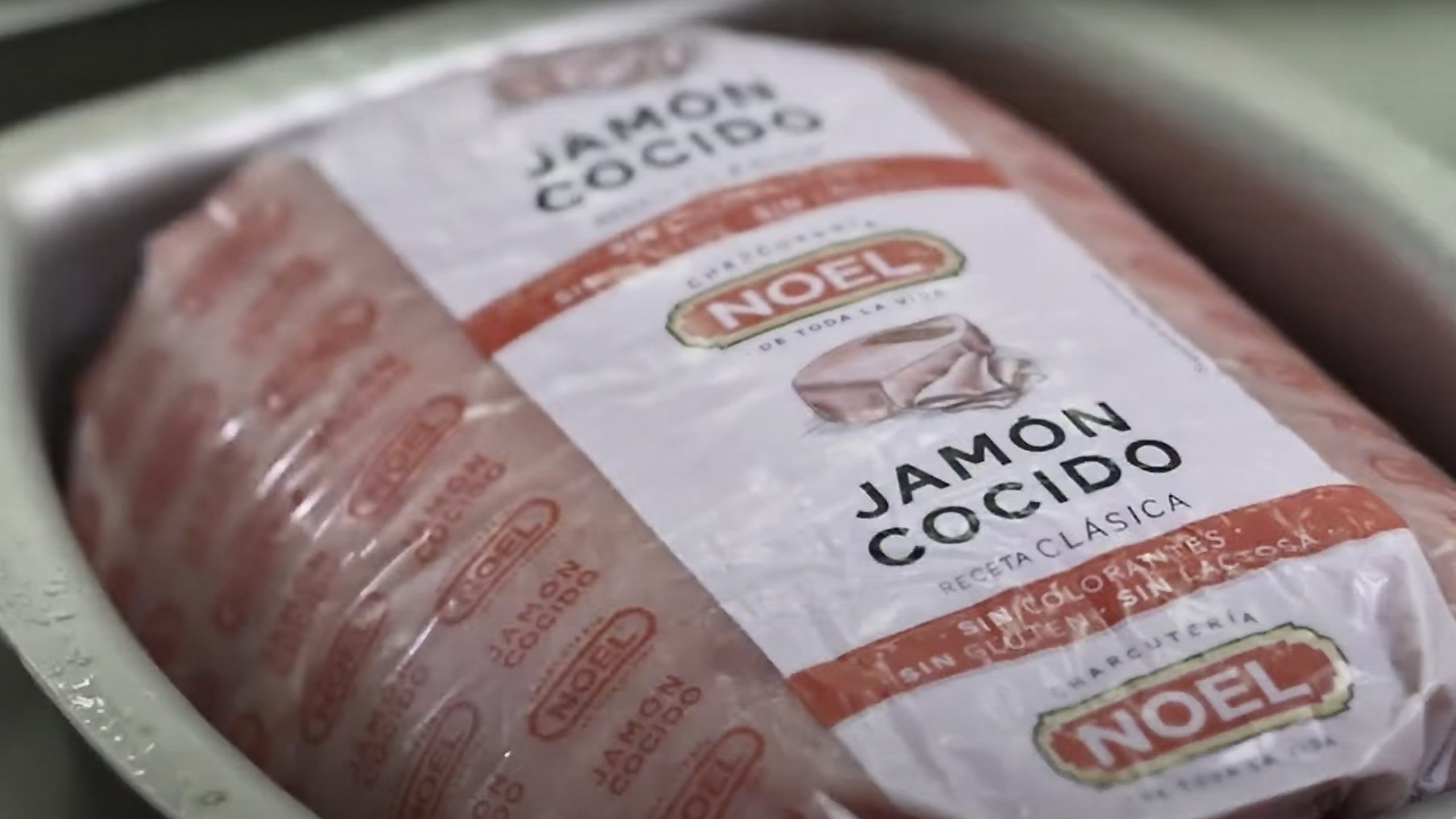
El año 2024 ha sido prolífico para la sección de ‘Casos de éxito’ en la plataforma de Atlas Tecnológico. No obstante, el calendario de 2025 también ha comenzado a llenarse de proyectos destacados de las empresas integrantes del ecosistema Atlas. Señalamos los éxitos de ESSS en el ámbito químico, MESbook en materia de telecomunicaciones e Imperia en el área alimentaria.
ESSS detectó y resolvió un problema que estaba entorpeciendo la productividad de Bayer, la histórica compañía químico-farmacéutica. El desafío residía en su proceso de tratamiento de semillas, concretamente, en la falta de control preciso sobre varias variables clave, que incluyen la aplicación de sus capas protectoras, las mezclas del lote o la detección del momento adecuado para concluir el proceso. Es decir, Bayer dependía de métodos experimentales tradicionales y carecía de sensores adecuados y tecnología analítica de proceso.
Es por ello que ESSS optó por herramientas de simulación para solventarlo, prototipos digitales del equipo para optimizar el diseño de tratamiento de semillas. Mediante la simulación, Bayer evaluó digitalmente más de 200 variantes de diseño, lo que les permitió identificar el más adecuado para mejorar el proceso de tratamiento de semillas. Así, el diseño validado aceleró también los ciclos de desarrollo del producto, al reducir los esfuerzos necesarios para realizar pruebas y prototipos. La simulación brindó a Bayer la capacidad de experimentar virtualmente con múltiples diseños, lo que resultó en un proceso de desarrollo más rápido y eficiente.
MESbook presenta un nuevo caso de éxito de la mano de GAZC. La compañía manufacturera implementó APQP Digital, un enfoque innovador que integra herramientas clave en la dinámica de fábrica al conectar máquinas, sistemas, procesos y personas en una única plataforma de gestión en tiempo real. Sus operaciones se transformaron por completo, al permitir reducir costes indirectos, mejorar la eficiencia operativa y aumentar la consistencia y calidad de los procesos productivos. Sin embargo, pese a las avanzadas tecnologías de programación recreativa, cachés en JSON y una arquitectura escalable SaaS, el proyecto presentaba desafíos.
Se enfrentaron al problema de garantizar latencias de comunicación inferiores a un segundo con los sistemas ERP, gestionar tiempos de respuesta en bases de datos SQL bajo alta demanda y controlar elementos físicos como transportadores y sistemas de clasificación en tiempo real. Además, la adopción del sistema por parte de operarios, supervisores y directivos requirió un robusto proceso de gestión del cambio, que incluyó formación personalizada, gestión de expectativas y un enfoque transparente para asegurar el éxito de la transformación digital.
Para abordarlo, MESbook diseñó un protocolo de comunicación basado en telegramas TCP (Protocolo de Control de Transmisión). La programación reactiva paralelizó procesos clave, incrementó la velocidad, la disponibilidad y la tolerancia a fallos. Además, se implemento un plan estructurado de gestión del cambio que incluyó equipos liderados por responsables internos, formación personalizada y seguimiento continuo, asegurando la adopción del sistema y consolidando la transformación digital.
Para Imperia SCM, la anticipación se convirtió en el motor de transformación para un líder de la industria alimentaria. Trabajaron con Noel, una empresa dedicada a la elaboración y comercialización de productos cárnicos que trabajaba con un ERP (Sistema de planificación de recursos empresariales) que no contaba con módulos de previsión de la demanda, compras y producción. Es decir, la planificación de sus operaciones se realizaba mediante hojas de cálculo de forma manual usando datos históricos. Esto dificultaba la gestión por la gran cantidad de plantas y líneas de producción de las que disponen.
Imperia reconoció en este problema un espacio en el que su software era idóneo para ponerle fin. Una vez implementado, se consiguió automatizar procesos, trabajar mejor sus datos históricos y utilizar algoritmos de cálculo avanzados, al analizar tendencias del mercado y realizar previsiones de demanda mucho más precisas. Al fin y al cabo, al anticiparse a las demandas del mercado, son capaces de producir mejor, gestionar sus compras y optimizar el stock. La traducción que se extrae de estos beneficios es un mejor servicio al cliente y la aportación de un valor añadido y adaptado a las necesidades y funcionalidades requeridas.